Stainless Steel Casting Surface Treatments
Investment casting can achieve good dimensional tolerances, excellent surface finish. Most machining can be saved. But sometimes, customers need a better surface finish. So Investment casting Surface treatment or surface finish becomes an important post-treatment method to smooth the casting surface. JC casting is professional in different surface finishes for investment castings. This experience enables our company to fulfill different surface treatment requirements.
Because stainless steel casting is our most output product, so let’s introduce stainless steel casting Surface Treatments mainly.
If you are interested in all Investment Casting Surface Treatments. You can check this article: Investment Casting Surface Treatments
Common surface finishes of stainless steel investment castings are l as follows:
1-Shot Blasting
Shot blasting is a surface treatment method by impacting steel balls on the stainless steel castings surface at high speed. This surface finish type can remove the oxide layer on stainless steel casting Surface. In all the surface finishes, shot blasting is the most common surface finish method. And the cost is also the cheapest.
2-Sand Blasting
Sand Blasting is a way to blast the stainless steel castings surface with fine sand. It can be ceramic or Glass beads.
The surface smooth of sand bead blasting looks better than shot blasting. But the cost is higher. If the casting has a higher requirement on the surface, sand blasting is recommended.
3-Pickling and Passivation
Both pickling and passivation are chemical treatments method. Its purpose is to remove contaminants and assist the formation of a continuous chromium-oxide, passive film.
Pickling is the way to drop surface dirt like oxide skin, rust, welding spots.
Passivation is a process that forming a new abundant chromium protective layer. In order to improve the anti-oxidation ability of stainless steel castings.
All the stainless steel castings will be cleaned by the pickling process at least.
4-Electropolishing
Electropolishing is to remove stainless steel casting surface tiny burrs. And it can improve the brightness and the corrosion resistance of stainless steel castings. It creates a lasting bright finish.
All varieties of stainless steel castings can be Electropolishing. After electropolishing, the stainless steel castings surface shows a silver color. It looks much more bright than before.
5-Brushed finish
The brushed finish is a uni-directional satin finish. It makes stainless steel cast parts a distinct look. It keeps a metal surface, but not all metallic luster. It also gives very fine pattern lines parallel to the brushing direction.
6-Vibratory Polishing
Vibratory Polishing is a process of mass production finishing. It is mostly used to burnish, degrease, clean, deburr, descale, radius, refine, dry. And offer pre-plate or pre-paint finishes of stainless steel castings.
Among all process applications. Vibratory Finishing is one of the most common styles of surface finishing. Compare to other deburring methods, Vibratory Polishing can prevent stainless steel castings from being bent or distorted.
7-Mirror Polishing
Mirror Polishing is a mechanical polishing process by workers. They polish stainless steel castings surface with various polishing machined by hand.
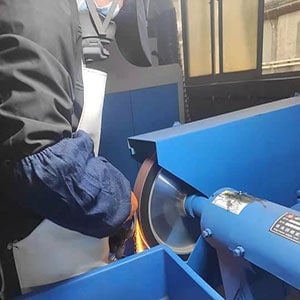
A mirror polished stainless steel casting surface can achieve a very smooth and bright surface finish. It looks like a mirror.
In the mirror polishing process, there are several procedures. They are grinding wheel polishing, hemp wheel polishing, and cloth wheel polishing.
The mirror polishing cost is the highest of other surface finishing methods. Especially for luxury products, it is used for high-end market applications.
8-PVD Coating
PVD coating is a surface finish way to color stainless steel castings.
Vacuum titanium coating requires a relatively smooth surface. After finished castings, the casting parts are better to mirror polished or electropolished. There are various colors for stainless steel castings. Such as gold, rose gold, etc.
JC casting
JC Foundry can supply all the above surface treatment processes. We can meet all your demands.
If you are not familiar with the differences between these surface finishes. We can provide an ideal solution for you. Or even supply samples with different surface finishing ways for your comparison.
Contact us for more solutions.