Today, we will talk about the theme of “What is Investment Casting”.In the article, you will get the below info. Hope it is useful for you to understand What is Investment Casting?
What is Investment Casting?
Investment casting refers to the general term for obtaining precision-sized castings. Investment casting is also called precision casting. Its products are precise, complex and close to the final shape of the part. It can be used directly without processing or with little processing. It is an advanced technology with near net shape.
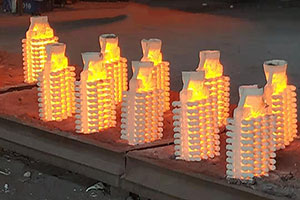
Compared with the traditional sand casting process, the casting size is more accurate and the surface finish is better.
It Mainly includes precision casting, ceramic mold casting, metal mold casting, pressure casting, lost foam casting, etc.
Investment casting History
Investment casting is an ancient technique. It can date back thousands of years. The typical casting products are art and even practical tools. Such as figures, complex tools, and arrowheads.
Although Investment casting has been used before the century. But its fast development is during 1940′. In World War II, the demand for precision net shape become high and strict. Traditional manufacturing methods can not meet its request. Its industrial importance and popularity grew.
After the war, Industry turned to investment casting. Especially the shell process using wax patterns that are from the United Kingdom. This method resolved the problem of wax removal by enveloping a completed and dried shell in a vapor degreaser. The vapor permeated the shell to dissolve and melt the wax. This process has evolved into the current process of melting out the virgin wax in an autoclave, or furnace.
These years, as per 3D printing technic development, it can replace wax patterns. The mold manufacturing cost is declining, and production time becomes shorter.
Learn more about the process of investment casting.
What is the investment casting process?
During the investment casting process, besides some main equipment, we still need to utilize metal mold, wax, ceramic slurry, furnace, molten metal. Below is the main process of investment casting production:
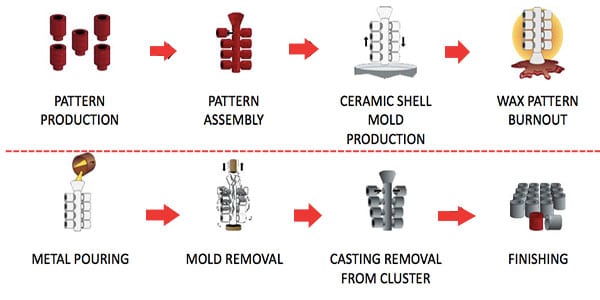
A: Tool design/build
- Produce and provide the same patterns as finished products.
B: Mounting The Wax Patterns And Creating The Tree
- Injects semi-solid wax using an automated process developed in-house for higher dimensional stability
C: Create Shell
- Dip wax pattern in a ceramic slurry, covered with sand stucco, repeat, and to dry.
D: Wax Removal
- The entire assembly is placed steam autoclave to melt away the wax.Then get a hollow cavity
E: Pouring
- Melting the metal to liquid, then pour into the shell hollow cavity
F: Shell removal
- By knockout the shell,to get the casting
G: Finishing
- As per quality request, blast cleaning, plating, painting, assembly, and machining can be done
H: Testing and Inspection
I: Packing and delivery
ps: For more investment casting process details, welcome view the https://www.investmentcastingpci.com/investment-casting-process/
There is an investment casting process description and investment casting process flow diagram with details. Or download process of investment casting pdf or investment casting process steps ppt
The above investment casting process is also called “wax lost investment casting”.For more investment casting methods, there are water glass investment casting and silica sol investment casting. We will also introduce them later.
What products can be investment casting?
- Carbon
- Alloy Steels
- Inconel
- Aluminum
- Stainless Steel
- Cobalt Alloys
- Super Alloys
- Carbon Steels
- Titanium
- Carpenter 20
- Molybdenum
- Tool Steel
- Monel
- Tungsten
- Nickel
- Waspaloy
- Hastelloy
- Zirconium
- Cobalt
- NX-188
- Nickel Aluminide
What is investment casting used for?
As one of the earliest casting methods, investment casting still has wide applications in commercial and industrial. This is also certified that the usage and technic life of investment casting. From founding to now, JC casting products ranges has enlarged to the medical, aerospace, military from the common construction hardware, machinery parts. We have been supplying high-quality, high-precision investment castings.
The following are some of the most common and relevant applications of investment casting:
- Aerospace
- Agricultural, Industrial & other Heavy Equipment
- food service, gas and oil, and energy industries
- Engineering components such as rotors and turbine blades in motors and generators
- Valve parts (casings, pistons, etc.)
- Mining Industry
- Military & Defense
- Medical Devices & Equipment
- Marine
- Hand Tools & Power Equipment
- Automotive/Truck Parts
- Door & Lock Security Hardware
Why do people use investment casting
When we ask why to use investment casting, we have to say the advantages or benefits of investment casting. Such as
- 1-Excellent surface finish, near net shape,no flash or parting lines
- 2–Complex shapes – intricate parts are castable, hollow passages and thin walls can be easily achieved.
- 3–High dimensional accuracy, tight tolerances
- 4-Almost any metal can be cast. Such as steel, nickel-based superalloy, titanium, and aluminum
- 5-Affordable tooling, faster production
You can view More advantages of investment casting…
When will we use of Investment Casting?
Investment casting has more requirements for the production process and labor. Investment casting is a relatively expensive process. But the benefits will outweigh the costs. Therefore, we need to consider the following factors when using Investment casting.
- No. 1: quality requirements.
If the product has very strict quality requirements. Such as dimensional accuracy and surface finish. Now, we can consider using Investment casting methods for production. Because precision casting parts with high precision dimensions are easy to get. And do not need secondary processing is required.
- No. 2: Mold cost and quantity.
Investment casting mold is a tool that can be used permanently. For products with low quantity requirements, the unit price of the product will be very high. One or even multiple molds is normal in Investment casting production. This front-end cost is very high. If the product quantity requirements are very large, then the cost of this mold can be spread evenly to each product. The cost of a single piece is negligible
- No. 3: Size requirements.
Although precision casting can manufacture castings of various sizes. But this ability is within a certain size range. Most of the time, the size of precision casting will be smaller than that of sand casting.
- No. 4: The time factor.
Investment casting will take more time-consuming than other casting processes. Mainly in the shell dring process. So, consider your own time requirements when considering precision casting. For products with small quantity requirements and fast delivery speed, 3D printing precision casting is a good choice.
Investment Castings Cost
Strictly speaking, the manufacturing costs of different investment castings in each process are not exactly the same. But, some details differences are small. It can be calculated on an average basis. What we are concerned about are those factors that have a greater impact on the cost of casting. The 6 main factors that cause the cost difference of the Investment Castings Cost are as follows:
1.Metal Material types
The cost will vary depending on the metal alloy. Among steel castings, stainless steel castings are the most expensive of high stainless steel. Compared to steel castings, cast iron parts are much cheaper due to the lower cost of iron alloys. Of course, for the same material, the cost may vary at different times. So, when the material cost is low, the purchaser will get a cheaper casting.
2. Production technology
Even investment casting parts can be manufactured in water glass investment casting and silica sol investment casting techniques. Silica sol casting will give investment castings better dimensional accuracy and surface finish. So the cost will be higher than water glass casting. Of course, water glass casting is more accepted by customers due to its lower production costs. But, if more precise tolerances and surface finishes are required, silica sol casting is preferred.
1) Confirm if the casting can be produced.
Precision casting plants need to check whether the blank casting process can be used to produce blank castings, and some may use wet sand. Some may use resin sand, shell casting, and automatic molding processes. Wet sand is cheaper and shell casting is the most expensive. Relevant factors include dimensional tolerances, surface quality, structural complexity, annual demand, weight, and size. These factors will affect the cost of the blank casting. Of course, if these processes fail to meet the requirements, precision castings will not be able to produce them.
2) Confirm whether the processing requirements can be met.
For normal processing work, most of the cast-iron mills with processing capabilities will be able to process. Otherwise, they will have to entrust other specialized processing workshops to process. It is not a good choice because the cooperation between precision castings and processing plants may cause more difficulties and delay delivery. Since the quotation needs to take into account the relevant processing equipment, working hours, and prices. So, the processing cost is difficult to calculate. Also, annual demand is also an important factor affecting processing costs.
3. Casting output
The casting yield is a percentage of the casting weight that the actual weight of the precision casting is.
For a specific precision casting, the yield is equal to the total weight of the precision casting on the same tree as a percentage of the tree weight. It is related to precision cast structures and group tree schemes. It can vary from 30% to 60%, mostly between 40% and 50%. The lower the casting yield, the higher the cost.
The relationship between the cost of the front section and the yield rate is the cost per kilogram of the front part of the casting = the cost of the previous section of the casting weight per kilogram. The cost of the front section of each kilogram of casting is inversely proportional to the yield. The lower the yield, the higher the cost of the precision casting before the unit weight. And the lower the yield, the more significant the impact. The cost of pouring the front section of each kilogram of molten steel is 6 yuan.
When the yield is 45%, the cost of the front section of each kilogram of precision casting is 13.33 yuan.
When the production rate is 30%, the cost of the front part of precision casting is 20 yuan/kg. It is 6.7 yuan higher than the average. The cost increased by 37.6%. The impact on the total cost of 304 stainless steel precision casting was about 17%.
When the production rate is 60%, the cost of the front part of precision casting is 10 yuan/kg. It is 3.3 yuan lower than the average level. Process costs are reduced by 18.5%. For 304 stainless steel precision casting, the total cost is reduced by about 7%.
Deriving the cost of the pre-casting section to the yield rate can be concluded. The rate of influence of the yield on the cost of the front section of each kilogram of precision casting is inversely proportional to the square of the process yield.
When the yield is 45%, for every one percentage point reduction, the cost per kilogram of precision casting increases by 0.3 yuan.
When the yield is 30%, for every one percentage point reduction, the cost of the front section per kilogram of precision casting is increased by about 0.67 yuan.
This shows that the impact of the yield on costs is very significant.
On the other hand, some precision castings, especially irregularly shaped thin-walled castings, are difficult to increase due to the limitations of the cast structure and the grouping scheme. This important factor should be taken into account when determining the price of precision casting.
4.Quantity of shell layers
Since the shape of the investment casting is always different. There will be differences in the building construction layer. For more complex structures, more shell layers will be needed, which will cost more. For example, casting with elongated holes or slots requires two or even three layers. It is usually enough to cast the back layer twice. Larger castings may need three or more layers. The cost per kg of precision cast shell is about 5.9 yuan. Among them, material costs accounted for 67.8%, fuel and power accounted for 23.9%, and wages accounted for 13.3%. At the cost of 4 yuan/kg of shell material. The consumption of zirconium sand and zirconium powder accounts for about 63%, accounting for 42.7% of the total cost of shell making. The cost of silica sol is about 12.2% of the cost of the shell. Although zirconium sand zirconium powder is only used for the top layer.
5. Purchasing Area
In China, although labor costs continue to rise, their costs are much lower compared to developed countries. It is very expensive to manufacture investment castings in Europe and the United States.
6. Other Cost Elements
Other costs include packaging costs, surface treatment, painting, inland and sea freight, exchange rates. These costs will be related to the specific needs of the customer.
How to Find an investment casting company that has a foundry.
JC Casting has its own foundry and machining factory. We are a top leader investment casting supplier and exporter in China. We obey a strict quality inspection process in its investment casting. We are ISO 9001:2008 certified and have the experience of helping you with all your casting needs. JC Casting has various alloy materials you may need. JC Casting can do titanium, steel, and iron casting, as well as aluminum casting. Our goal is 100% on-time delivery. We guarantee that all services purchased are high-quality materials. It is also very affordable.
We hope that the information given here will enlighten you. You will now have a better understanding of titanium investment casting. You can now choose what you need. To know more you can visit our website at https://www.investmentcastingpci.com/. Send us an email at [email protected].
PS:
The above is some info about what is investment casting? For more articles about investment casting articles, you can view below articles list:
- What products can be investment casting?
- What materials can be used in investment casting?
- The advantages and disadvantages of investment casting?
- Different investment casting methods.
- Investment Casting Purchasing Guidelines
- Investment Castings Cost