What is Gray iron castings?
What is Gray iron casting? Gray iron casting, also called Grey Iron Casting, is a casting part that is typically made by smelting grey iron. It is one kind of Iron Casting. Grey iron is an alloy made of iron and carbon. It also possesses traces of phosphorous, sulfur, silicon, and manganese. Grey iron or grey cast iron is a material type of cast iron with a graphitic microstructure. So it is called grey iron because of the gray color of the fracture.
Gray iron can meet specific requirements for hardness and wear. The heat treatments can yield even higher mechanical properties. It has features of high thermal conductivity, strength, durability, machinability, and low cost. So grey iron is widely used for valves, engine blocks, brake drums, pump housings, and cast-iron cookware.
Gray iron casting is finished in a foundry. Gray iron castings are made by pouring molten iron alloys into molds. The finished iron casting may be machined. But grey iron cannot be forged or extruded at any temperature. So it must be cast.
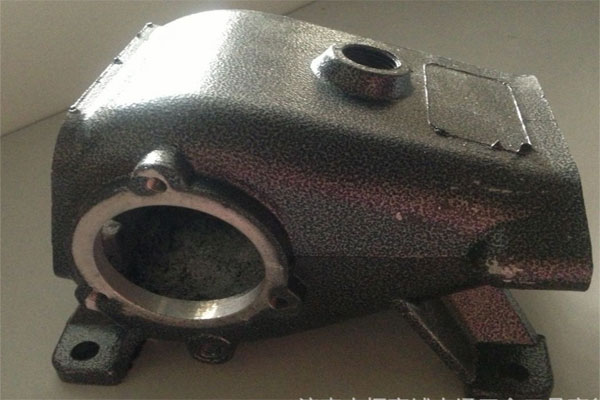
Gray iron casting, also to be wroten in Grey Iron Casting, was produced by the Chinese over 2,500 years ago. It is widely used in stoves, common household goods, tools, building materials, and statuary. Today, we are a modern Grey iron castings foundry company in China. Most of our Grey iron castings are exported all over the world. In this article, we will introduce the WHAT IS THE GRAY IRON CASTINGS? ITS PROCESS, BENEFITS, TYPES, AND SIMILAR PROCESS OF CASTING.
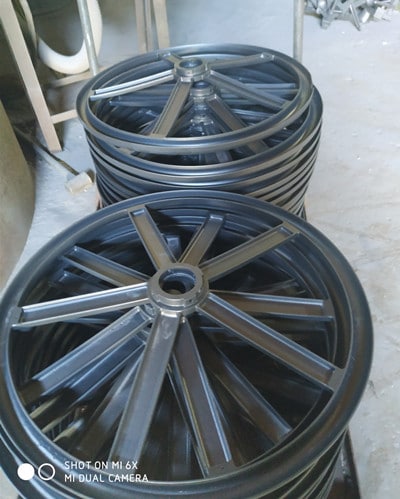
Our main process method of Grey Iron Castings
Commonly used grey iron castings process in the market is produced by sand casting. In our foundry, we can make grey iron castings in two types:
Type 1: Lost Foam Casting
The only investment casting process for cast iron components, which has lots of advantages to produce small gray iron investment castings, such as saved mold cost, shorten the production cycle and improve production efficiency. With the lost foam casting process, we can help our customers to obtain high accuracy products with excellent surface finish, and fewer machining operations will be done.
Type 2: Resin Sand Casting
The main sand casting process for small and medium castings. Compare with other sand casting processes, resin sand casting is a relatively precise casting method close to investment casting. As good rigidity of resin sand and high strength of sand mold when early casting, then we could effectively eliminate the shrinkage cavity, shrinkage defects of gray iron castings.
Heat Treatment of Grey Iron Castings
Most of the time, grey iron castings are supplied to our customers in the as-cast condition directly. But For some purposes, gray iron castings can also be heat treated, such as to relieve residual stresses, improve machinability, increase the hardness of the surface either through induction or flame hardening, or harden the entire section through an oil quench and draw treatment. Such heat treatment will not change the graphite structure. Although the graphite may increase in volume if a pearlitic iron is completely fertilized, in which case, the graphite is usually deposited on the flakes originally present. The matrix however is quite responsive to heat treatment just as in the case of steel.
Machining Capability of Grey Iron Castings
Grey iron supply a hardness level that is machinable. With machining facilities in-house, we can do machining also after casting. Once our customers have machining requirements on grey iron castings, it will be best to supply us with both casting and finished drawings. Our engineering team will strictly machine products referring to the machining drawings. Our machining capability can greatly reduce additional costs for our customers.
Grey iron casting is used in many market segments, including automotive, agricultural, machinery building, electronics, irrigation, ventilation, architecture, construction, and transportation industries.
The typical finished Gray iron casting products.
Grey iron castings are frequently used to make: valves, cases, engine blocks, dies, pump housings, pipes, brake drums, decorative embellishments and grey cast iron cookware.
Benefits of Grey Iron Castings
There are a number of important benefits that the use of Gray Iron for casting provides. Gray Iron Castings can be:
The high carbon content for melting, weld, the machine easily. |
Low shrinking during the casting process. |
Corrosion-resistant |
High conductivity, ideal for cookware. |
Machined more easily |
Used in applications that require high strength to weight ratios |
Dimensional stability |
Produced economically in high volumes using disamatic equipment |
Gray iron casting Applications
Gray iron casting is used in many market segments, including automotive, agricultural, machinery building, electronics, irrigation, ventilation, architecture, construction, and transportation industries.
Gray iron castings are the optimal choice for the construction of highly durable and strong products.
As per its grade or class:
Class 300 Gray Iron | For the production of beds, gears, cylinder blocks, heavy-duty machine tools, high-pressure hydraulic components, cylinder heads, bushings, piston rings, etc. |
Class 200 and Class 250 | For manufacturing cylinder bases and liners, brake wheel, gearboxes, coupling plate, flywheel and pressure valves. |
Class 100 and Class 150 | For creating hammers, pipes, pulleys, protective covers, handwheels, bearings, and pumps. |
Gray iron castings are the most widely used type of cast iron. China foundry is the best choice for parts from Gray iron casting. If you have any inquiry of it, kindly contact us freely.
Variations and Similar Processes
Different grey iron casting processes include centrifugal casting, die casting, sand casting and ductile iron casting.
Centrifugal casting is a method used to cast cylindrical parts and components that produce fine-grained outer surfaces with even dispersion. To work, liquefied grey iron is poured into a mold that rotates at high speeds as it is introduced. Centrifugal casting stands apart from many other types of casting because it is mainly used to create stock materials for further machining, as opposed to parts shaped for specific applications. Grey iron castings made via this process can also be almost any diameter, length, and thickness.
https://www.youtube.com/watch?v=ZxVA-htTunU
Die casting is popular for a continuous cycles or the fast production of castings. It uses reusable molds that are made in the shape of the desired finished product. To die-cast the metal, manufacturers must inject it into the die and apply pressure. Die casting is good for use with small to medium parts that require good dimensional stability, carefully produced details, and good surface quality.
Sand casting, or sand molding, is a low-cost and low-maintenance casting option that uses a sandy mixture as a mold. The four main mixtures from which manufacturers may choose are called no-bake, dry sand, skin-dried, and green sand.
• No-bake molds are disposable molds, made of sand, a quick-setting resin, and a catalyst. They are formed with the help of a casting flask, which is usually made out of plastic, wood, or metal. No bake molds employ a heat-free, cold-setting casting process.
• During dry sand molding, unbonded sand is mixed with an adhesive or a chemical binder, shaped to form a mold and then baked a certain temperature to finish. To make castings, molten grey iron is poured into the mold, taking its shape.
• To create a mold using the skin-dried molding method, also known as air-dried molding, operators mix water, sand, a binder like clay and bonding additives and then dry it with a torch or heating lamp.
• Green sand molds are made the same way, minus the bonding additives and the heat drying.
https://www.youtube.com/watch?v=K8SYhISGxN4
Ductile iron casting, also known as spheroidal graphite casting, SG iron casting, or nodular iron casting, was developed in 1943 by Keith Mills. This process involves melting and casting ductile iron (iron alloys with controlled microstructures) along with one of the elements that make it ductile. This is usually either magnesium, cerium or yttrium. Ductile iron castings are not only more ductile than grey iron castings, but also have higher tensile strength than gray iron castings. Because of the high tensile strength and ductility it produces, ductile iron casting is used to produce: water pipes, sewer pipes and components of windmills, tractors, trucks and cars, piano harps, and oil rigs.