Cast iron
What is Cast iron ?
Cast iron is a ferrous alloy of iron, carbon, and silicon. With carbon content of 2.1 to 4.5 % and silicon at about 2.2% and a small amount of Sulphur, Manganese and Phosphorous.
Iron casting is one of the oldest casting methods in the world. The cast iron is melted and poured into molds or casts to make a part of products of desired size and shape. Cast iron can be used in a range of industries. In the Manufacturing Process of Cast Iron, the alloying elements determine cast iron type. Compared with steel casting, iron casting has a wide range of advantages of its properties.
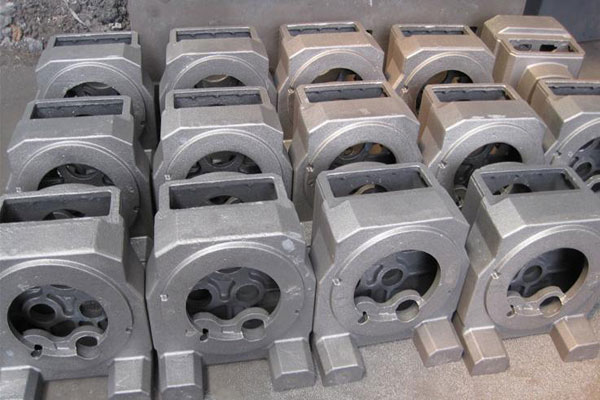
The advantages of Iron Cast
- Good casting properties(low Tm, good fluidity).It can be given any complex shape and size without using costly machining operations
- Good machinability (graphite cast irons)
- Low Cost
- Strong compression strength compared to steel
- Excellent anti-vibration (or damping) properties hence it is used to make machine frames
- Good Sensibility
- Excellent resistance to wear
- Constant Mechanical properties between 20 to 350 degree Celsius
- Very low notch sensitivity
- Low stress concentration
- Durability,Resistance to deformation
The types of Iron Cast
The Iron Cast main types are Grey Iron, Ductile Iron, Compacted graphite, White, Malleable, Abrasion-resistant, Nodular or spheroidal, Austenitic. Here we make a brief introduction in the below table.
Types | Properties |
White cast iron: Carbon is present here in the form of Iron carbide (Fe3C). | High compressive strength Difficult to machine Good hardness Resistance to wear |
Gray cast iron: Carbon here is mainly in the form of graphite. It is inexpensive. | Good machinability Good resistance to galling and wear High compressive strength Brittle |
Ductile cast iron | High ductility High strength |
Malleable cast iron They are made malleable with the help of annealing. They are used to make parts where forging is expensive like brake supports, hubs of wagon wheels, etc. They are inexpensive. | High ductility Tougher than gray cast iron Be twisted or bent without fracture Excellent machining capabilities |
Nodular or spheroidal cast iron Here graphite is present in the form of spheres or nodules. | High tensile strength Good elongation properties |
The applications of Iron Casting
The iron cast is the main raw material for Iron casting. It has wide applications.
- Automotive parts
- Cookware and utensils
- making anchor for ships.
- Stoves and firebacks
- Cast Iron Piping Pluses
- Engine Block Comeback
- Hardware, hinges, latches
- Columns, balusters,Stairs
- Decorative features,Fences
- Tools and utensils
Iron Casting Process in our foundry
Like other investment castings, there are also different producing methods of iron castings. In our Iron cast foundry, there are 2 main methods for iron casting: sand casting or lost foam casting method.
Sand Casting
Also called sand molded casting. Is the process that utilizes non-reusable sand molds to form metal castings. Sand casting is used to produce a wide variety of cast iron components with complex geometries. In China, there are three types of sand casting techniques to make iron castings. They are precoated sand casting, resin sand casting, and clay sand casting.
Among them, precoated sand casting is the most precision sand casting process with general casting tolerance CT8. It can produce iron castings less than 2kgs. Clay sand casting is the second precision casting process with general casting tolerance CT9. Iron castings between 2kgs-60kgs are available in this method. And resin sand casting is mainly used for the production of large iron castings above 60kgs.
Lost foam casting
Lost foam casting is another casting technique for iron castings. It is a type of evaporative-pattern casting process that is like investment casting. But replace the wax with foam for the pattern. The advantage of lost foam casting is that the boiling point of foam is low. This helps to simplify the investment casting process by removing the need to melt the wax out of the mold. Cast iron is one of the commonly cast materials in the lost foam casting process.
With lost foam casting, we can make small iron castings with good dimensional accuracy and surface finish. For large iron castings, sand casting is the primary choice.
The common Cast Iron used for Iron Casting and standards:
Cast Iron Standards | GB | AWS | BS | NF | DIN | ISO |
Grey Iron | HT200 | No.30 | Grade 220 | EN-GJL-200 | GG20 | 200 |
Grey Iron | HT250 | No.35 | Grade 260 | EN-GJL-250 | GG25 | 250 |
Grey Iron | HT300 | No.45 | Grade 300 | EN-GJL-300 | GG30 | 300 |
Grey Iron | HT350 | No.50 | Grade 350 | EN-GJL-350 | GG35 | 350 |
Ductile Iron | QT450-10 | 65-45-12 | GGG-40 | EN-GJS-450-10 | 450/10 | 450-10 |
Ductile Iron | QT450-18 | 60-40-18 | GGG-40 | EN-GJS-450-18 | 400/18 | 450-18 |
Ductile Iron | QT500-7 | 80-55-06 | GGG-50 | EN-GJS-500-7 | 500/7 | 500-7 |
China Iron Casting manufacturer and exporting Company
Our Iron Casting Company, founded in 1997, has a long history of iron casting production in China. Our equipment and plant facilities keep continuing to upgrade. So we can provide our customers with the highest quality products with our latest lost foam casting and sand casting technology. Based on the advantages of iron cast, we can reduce production time. Shorten the delivery time, save your iron casting cost. Enhance your competitive ability in the iron castings market.
On the Technic, we have a knowledgeable and experienced team. On the management, we obey the ISO quality control system. Each inquiry will be answered professionally. If you have any casting projects or inquiries, Contact us now to get a free quote.
The Iron Castings
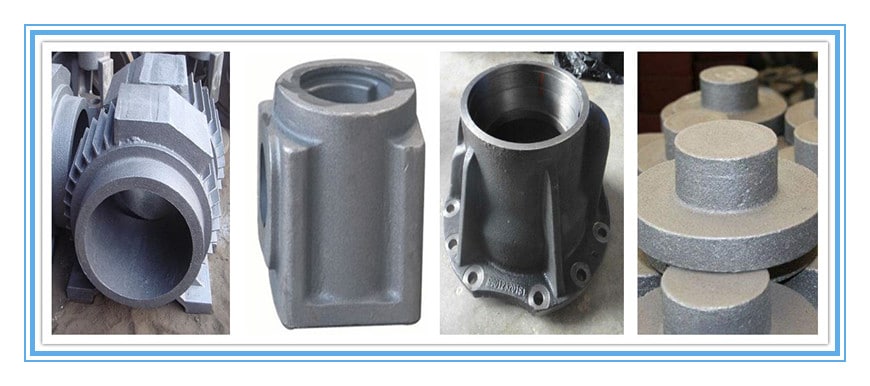