What is Titanium Investment Casting
Titanium investment casting is a manufacturing process that uses titanium. It replicates the exact shape of an item. Melted titanium poured into a wax pattern mold. Specialized ceramic material is then coated into the wax pattern mold and left to dry and harden. The wax pattern mold is then inverted and heated to let the wax melt and drip out of it. The ceramic shell becomes a superfluous investment mold. Liquefied titanium is then poured into the mold and cooled off. The mold is then broken off to reveal the replicated item.
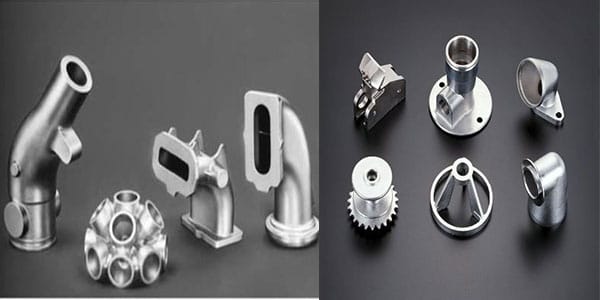
Why use Titanium?
Besides being durable, Titanium is also light and sturdy. It is resistant to corrosion. It is very reliable in creating consumer products as well as sporting goods. It is the ninth most abundant metal in Earth’s crust. In 1979, William Gregor discovered it to be a mixture of magnetite. He called it “manaccanite” for the parish he discovered it with. It was later confirmed by Martin Heinrich Klaproth that the manaccanite contained titanium.
Titanium is a transition metal. It can form bonds using electrons and shares the same features as copper, gold, and mercury.
Advantages of using Titanium in Casting
- It is as strong as most common steels with less than 40% of the counterpart’s weight
- It is corrosion resistant and almost as chemical attack-resistant as platinum. Titanium is one of the best metals used for ocean and chemical handling components.
- It has a very nice cosmetic appeal. Titanium’s cosmetic and technological appeal surpasses other precious metals. Titanium can is a gray-silver metal. It can be anodized into several colors as well as treated to give a glossy durable black diamond look.
Disadvantages of using Titanium in Casting
- Titanium is very difficult to cast. A zirconium oxide ceramic mold is used to harness the titanium’s full potential.
- It is very rare. It is very hard to find so it is generally more expensive than other types of metals like iron, steel, or aluminum.
Titanium has its pros and cons. It is strong, durable, and corrosion-resistant thus outweighing its expensive state.
Titanium Features and Properties
- Durability. To a fault, titanium is impervious to the daily grind of wear and tear. Thus, it increases the service life of the equipment it is used for. It is resistant to cracking or bending and is capable of being resistant to scratches. Stone settings in titanium resist loosening very well. Titanium’s high strength allows innovative and more delicate stone settings. More than your traditional jewelry metals.
- Lightweight Strength: Titanium displays the highest strength-to-density ratio for any metal. It also provides the same amount of strength as steel at 40% of its weight.
- Corrosion Resistance. It protects itself from rust or corrosion. Rust affects other metals like aluminum, iron, and steel. This is because of the thin layer of titanium oxide created on its surface when exposed to oxygen.
- Temperature Resistance. It is valuable to the medical, aeronautics, and industrial fields. This is due to the titanium’s high melting point (1,668 Celsius or 3034.4 Fahrenheit).
Main applications of Titanium Investment Cast parts
- Aerospace Industry. Airline industries have been using titanium in building their engine parts. Not to mention their planes’ landing gears, frames, hydraulic sections, and many more.
- Medical Industry. Titanium is used in biomedical applications. Hip, knee, and dental implants, reconstructive pins, and prosthetics have been the beneficiaries. This is because of its high strength-to-weight ratio. And also its compatibility with human tissue or hypoallergenic properties. It is used in manufacturing surgical instruments like scissors, scalpels, forceps, and knives.
- Military and Security Sectors. Titanium invested casting parts are currently used in military and naval ships.
- Oil and gas industries, transportation sector, construction, consumer and sporting products use titanium.
Titanium Investment Casting Process
- A pattern or mold of the desired part is created from melted wax or plaster.
- The mold is coated with zirconium oxide. The standard ceramic mold cannot be used due to the chemical reaction it makes with the melted titanium.
- Once the ceramic mold shell has been completed. The wax is melted and drained out, leaving a hollow mold casing.
- Titanium is melted using induction in a water-cooled copper crucible. It is placed in a specialized heating container system. It prevents the titanium from being exposed to elements like nitrogen and oxygen.
- The melted titanium is now coursed into the specialized ceramic molding. Centrifugal force to fill in the void within the thin walls
- The titanium freezes into its solid form upon contact with the ceramic molding. Now it is ready to replicate the desired part or component needed almost immediately.
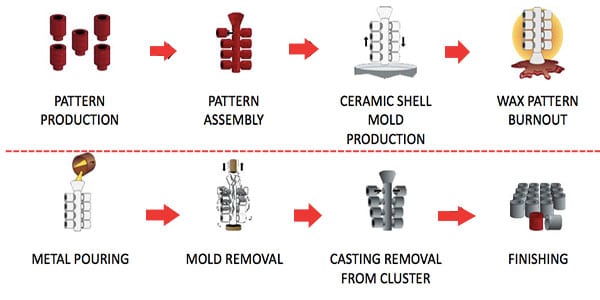
Why JC Casting is the right choice for your Titanium Investment Castings supplier
As a Titanium Investment Casting supplier,JC Casting implements a strict quality inspection process in its titanium investment casting. We are ISO 9001:2008 certified and have the experience of helping you with all your casting needs. JC Casting has various alloy materials you may need. JC Casting can do titanium, steel, and iron casting, as well as aluminum casting. Our goal is 100% on-time delivery. We guarantee that all services purchased are high-quality materials. It is also very affordable
We hope that the information given here will enlighten you. You will now have a better understanding of titanium investment casting. You can now choose what you need. To know more you can visit our website at https://www.investmentcastingpci.com/. Send us an email at [email protected].