What is Sand Casting
Sand casting, known as sand molding casting, is a casting process that uses sand as a mold. Then pour the liquid metal into this mold to create a casting part.It is one of the oldest casting processes. It can be used to make metal components of all sizes, ranging from 1kg to hundred tons. The statistics show more than 61% of all metal castings are produced by sand casting.
In modern industry, the sand casting Process controls, material options, tolerance capabilities, the ability to produce elaborate parts, broad size ranges have all come a very long way. It has several unique advantages.
The advantages of sand casting
- Suitable for more metals types.
- Can be for large size, Complex shapes sand casting products
- Compare with other metal forming processes, Tooling and equipment cost is low
- Scrap metal can be recycled
- Short lead time
The disadvantages of sand casting
- Sand casting has porosity, causing a low final part strength
- The surface finish is not good, need clean
- The cooled metal has shrinkage, which causes the dimensional accuracy to be poor.
- Low tolerance products need secondary machining
Although sand casting is a cheaper alternative to another investment casting. And can offer more complex shapes products. It needs time to get the same accuracy, finish, and overall part quality.So what product is better for sand casting?
Sand casting Applications
The sand casting process makes it ideal for almost any complex part.
Here we list its applications in different industries.So you can see how varied the possible applications can be.
- Many kinds of pistons and valves
- Blowers/impellers
- Cams, bushing, and bearings
- Electronic equipment
- Engine blocks
- bearings
- blowers & impellers
- electronic equipment
- gears
- machine parts
- mining machine parts
- oil pans
- pump bodies, pistons
- screw nuts
- trailer parts
- truck chassis parts
- valves
- water jackets & crankcases
- Automobile parts
- Screws, nuts, and gears
- Agricultural machines
- Medical equipment
Although sand casting is the oldest casting process. It’s basic producing technic no change. Just like to create a cavity in the parts shape then pour molten metal into it to get finished products. This is the most available and the most widely used metal casting method.
Next ,we will introduce how to Make a Sand Casting.
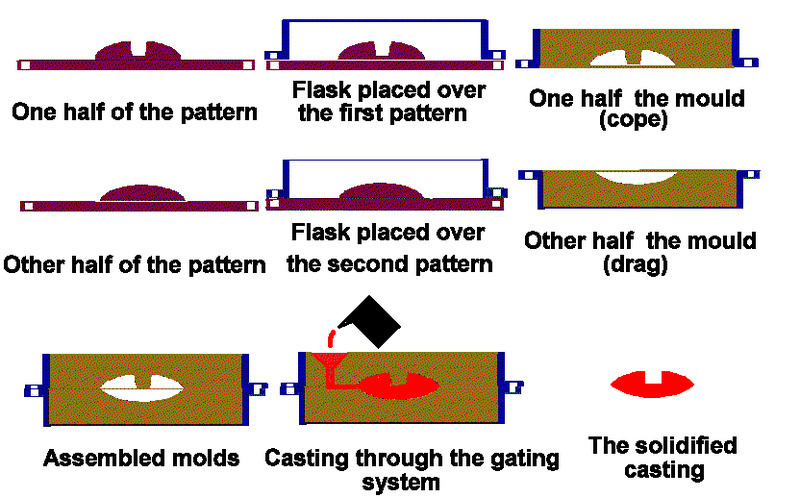
Image credit: https://en.wikipedia.org
The Sand Casting Process
The sand casting process is a casting method in which sand is used as the main modeling material to prepare molds. sand casting has characteristics of not limited by the shape, size, complexity and alloy types of the parts. So the production cycle is short and the cost is low). Therefore, sand casting is still the most widely used casting method in casting production. Especially single-piece or small-batch castings!
The basic process of the traditional sand casting process has the following steps: sand preparation- mold making- core making, modeling-pouring-sand falling- grinding processing- inspection, etc.
Sand mixing
Preparation of molding sand and core sand. For modeling. Generally, a sand mixer is used to mix the old soil and the appropriate amount of clay.
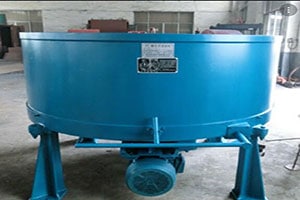
Molding
Make molds and core boxes according to parts drawings. Generally, a single piece can be made of wood molds. And mass production can be used to make plastic molds or metal molds. (Commonly iron molds or steel molds is more). Large batches of castings can be made into stencils. Now the molds are basically engraving machines. So the production cycle is greatly shortened, and it usually takes 2-10 days to make the mold.
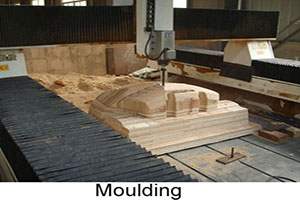
Core-making
Including modeling (forming the cavity of the casting with molding sand), core-making (forming the inner shape of the casting). And mold matching (putting the core into the cavity, and closing the upper and lower flasks) ). Modeling is a key link in casting.
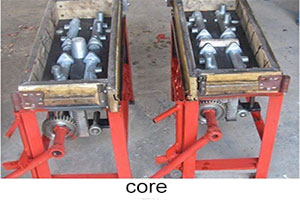
Melting
Distribute the chemical composition according to the required metal composition. Choose a suitable melting furnace to melt alloy materials. Form a qualified liquid metal liquid (including qualified composition and qualified temperature). Electric furnaces are generally used for smelting.
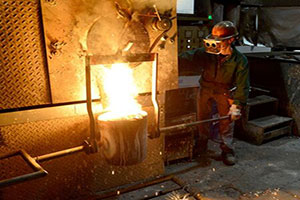
Pouring
Use a ladle to pour the molten iron in the electric furnace into the finished mold. Pay attention to the speed of pouring molten iron. Let the molten iron fill the entire cavity. Besides, pouring molten iron is more dangerous, so pay attention to safety!
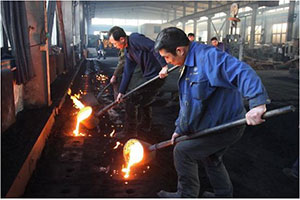
Clean-up
After pouring and waiting for the molten metal to solidify, take a hammer to remove the gate and shake off the sand of the casting. Then use a sandblasting machine for sandblasting. This way the surface of the casting will look very clean! The casting blanks that are not strictly required can basically be shipped after inspection.
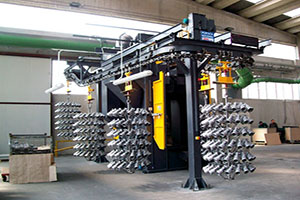
Casting processing
For some castings with special requirements or some castings that cannot meet the requirements. May require simple processing. Generally, a grinding wheel or a grinder is used for processing and polishing to remove burrs. Make the castings smoother.
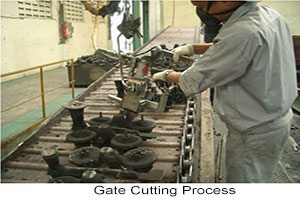
Casting inspection
Casting inspection is generally in the process of cleaning or processing stage. The unqualified ones are generally found out. However, some castings have individual requirements and need to be inspected again. For example, some castings require a 5 cm shaft to be inserted into the center hole, so you need to take a 5 cm shaft and try it out.
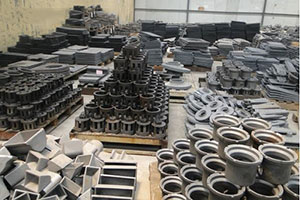
Conclusion.
After the above 8 steps, the casting is basically formed. For castings that require high precision, machining is required. With the development of casting technology, traditional sand casting is either improved or replaced by other casting methods. Constant innovation is the eternal theme. It is the inner quality and foundation that must be possessed as a casting perso
What materials can be used in Sand Casting?
Sand casting is almost available for any alloy, including high melting temperatures steel, nickel, and titanium.
Aluminum alloys, Brass alloys, Cast iron, Cast steel are The four most common materials that are used in sand casting.
Such as Aluminum 713 (Tenzaloy) Aluminum 535 (Almag 35) Aluminum A357Aluminum 319 Aluminum A356 Aluminum A355Brass C95400Brass C95300Brass C92600Brass C93700Brass C87500 Brass C83300 Red Brass Brass C83600 Red Brass Brass C89833 Lead-FreeAlloy C92200 (Navy M)Alloy C93700 (80-10-10)Alloy C87500 (Silicon Bronze) Alloy C95300 (415 B) Alloy C95400 (415 C) Alloy C95500 (415 D)
JC Casting -The Sand Casting supplier from China
JC Casting is a Sand Casting supplier from China. Introduction to the advantages of sand casting process:
Main products: mining machinery, auto parts, rail transit, food machinery, fluid chemical industry, engineering machinery, petroleum equipment, industrial locks and other castingsCompany specialty: professional casting + machining
Material type: low alloy steel, high manganese steel, wear-resistant cast iron, ductile iron, gray iron, stainless steel, carbon steel, heat-resistant steel, etc.
Application areas: automotive industry, rail transit, food machinery, fluid chemical industry, engineering machinery, mining machinery, petroleum equipment, industrial locks, aerospace, etc.
Casting process: silica sol precision casting, water glass precision casting, resin sand casting, lost foam casting, V method casting
Unit weight range: sand casting minimum 1 kg to maximum 25T
Machining: CNC
Heat treatment: solid solution, normalizing, annealing, quenching and tempering, carburizing treatment
Our products have been used in auto, casting, Agricultural, Medical equipment, chemical field already. If you have any inquiries about sand casting products, contact us!