What is Electroplating ?
Electroplating is a process of plating a thin layer of other metals or alloys on certain metal surfaces by electrolysis. Electroplating is mainly used to change the physical properties of an object.
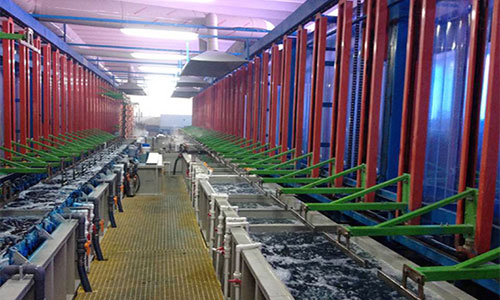
This process can prevent metal oxidation (such as rust). Improve wear resistance, electrical conductivity, light reflectivity, corrosion resistance (copper sulfate, etc.). Enhance aesthetics. Extend the useful life of the metal underneath the electroplated metal.
Of course, it’s also used to make gold and silver plated jewelry and knickknacks. This can give less expensive materials a better finish to enhance the product’s visual appeal. Many coin’s outer layers are also electroplated.
In the electroplating process, the plated metal or other insoluble material is the anode. The workpiece is used as a cathode. The cation of the plated metal is reduced on the surface of the workpiece to be plated to form a coating. In order to eliminate the interference of other cations, the plating layer is uniform and firm, and a solution containing a plating metal cation is required as a plating solution. In order to keep the concentration of the plated metal cations unchanged.
Why do we use electroplating? (The Purposes of Electroplating)
The main Purposes of Electroplating is for better Appearance,Surface Protection, Special surface propertie, Engineering or mechanical properties.
Sometimes finishes are only for decoration.Metals such as gold and silver are plated for decoration. It is cheaper to have gold- or silver-plated jewelry than solid items made from these heavy, expensive, precious substances.Metals of tin and zinc are plated to give them a protective outer layer.For example, food containers are often tin-plated to make them resistant to corrosion. For the same reason, while many everyday items made from iron are plated with zinc.
Some forms of electroplating are both protective and decorative. For example, Car fenders were once made from tough steel plated with chromium. It makes them both attractively shiny and rust-resistant.
Electroplating Applications
There are many aspects of electroplating applications, and the basic applications are three categories. That is, protective applications, decorative applications, and functional applications.
(1) Anti-corrosion. A metal layer is plated with a metal that is more resistant to corrosion than the metal itself. For example, a galvanized sheet is a layer of zinc plated on the iron plate. Improve the corrosion resistance of iron plates; there is also the plating of cadmium. It is also a widely used corrosion resistant coating. For example, the wheel rim of a bicycle is such a process; there is also nickel plating and the like.
(2) Decoration. Many of the metal parts we use every day look very bright. In fact, the surface is coated with a layer of nickel. Such as the bathroom faucets we bought, door handles and so on. For example, gold plating, some fake gold surface is coated with a layer of gold or copper.
(3) Performance. Some materials have no special properties, and plating on the material indicates the formation of a coating with this property. These materials have this special property. As we know, plastic is not electrically conductive, but some special requirements require plastic to conduct electricity. A special process is then used to coat the surface of the plastic with a layer of conductive metal. This plastic has electrical conductivity.
The purpose of electroplating is to plate a metal coating on the substrate. Change the surface properties or dimensions of the substrate. Electroplating enhances the corrosion resistance of metals. Increase hardness, prevent wear, improve electrical conductivity, smoothness, heat resistance and surface appearance.
The electroplated layer is more uniform than the hot dip layer and is generally thin, ranging from a few microns to tens of microns. By electroplating, decorative protective and various functional surface layers can be obtained on mechanical articles. It also repairs worn and machined workpieces.
ELECTROPLATING IN DIFFERENT INDUSTRIES
No matter you are looking for corrosion protection, improved durability, or increased electrical conductivity. Electroplating can provide solutions. That’s why electroplating is widely used in a variety of industries.
Here is the list of the industries that used electroplating and how do they work.
1) Automotive industry. Plating is commonly used in the automotive industry. It can prevent corrosion in harsh environmental conditions. Zinc-nickel plating solutions help prevent rust formation. And the electroless nickel plating plays as a great alternative for chrome on catalytic converters and plastic parts.
2) Electronics industry. Electronics companies often use gold plating to improve their conductivity.
Widely used to semiconductors and connectors. Copper plating is another commonly used metal in this industry. It can be used as an alternative to gold. When their focus is on conductivity. Palladium alloy is also used as protective coatings on electronic equipment and components.
3) Medical industry. The medical equipment industry often uses metal electroplating to improve the biocompatibility of components. Especially for implants. Gold, silver, and titanium are commonly used in this industry for their biocompatibility, corrosion resistance, hardness, and wear resistance. All of them are essential for implants and joint replacements.
4) Aerospace industry. Nickel plating is used in this industry to protect against corrosion and wear. And copper is used to improving heat resistance.
5) Oil and gas industry. Due to the nature of petrochemicals, Corrosion protection is a primary concern of the oil and gas industry. Electroless nickel plating is usually used in this industry to help protect piping and other components from corrosion. It helps improve the life of parts.
6) Many other industries. Such as the firearms, military, and defense industries. They are also use electroplating in various applications. All of these industries favor electroplating. Because of its functional capabilities, as well as its low cost and flexibility of application.
What products need electroplating?
- Sanitary ware and accessories
- Motorcycles, auto parts and steel furniture
- Locks, lighting and decorative hardware
- Plastic
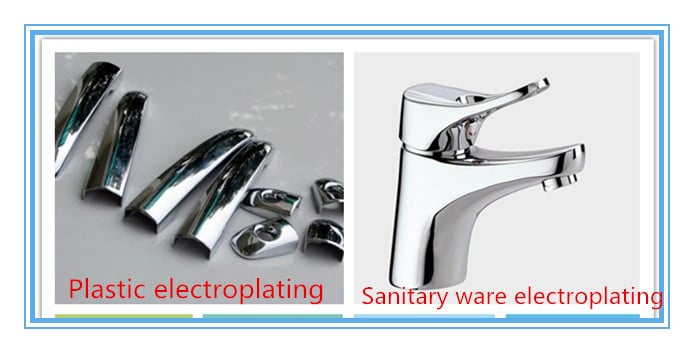
There are different roles depending on various plating needs. Examples are as follows:
1. Copper plating: used as a primer to improve the adhesion of the plating layer and the ability to resist corrosion. (Copper is easily oxidized. After oxidation, the patina is no longer conductive. So copper-plated products must be protected by copper.)
2. Nickel plating: base or appearance, improve corrosion resistance and wear resistance. (where chemical nickel is more resistant to chrome in modern processes). (Note that many electronic products. such as DIN heads and N heads. no longer use nickel as the base. Mainly because nickel is magnetic, which affects the passive intermodulation in electrical performance)
3. Gold plating: Improve the conductive contact resistance and improve signal transmission. (Gold is the most stable and expensive.)
4. Palladium-plated nickel: Improve the conductive contact resistance. Improve signal transmission, and wear resistance higher than gold.
5. Tin-plated lead: Improves the welding ability and is quickly replaced by other substitutes. (Because lead is mostly changed to bright tin and matte tin).
6. Silver plating: Improve the conductive contact resistance and improve signal transmission. (Silver has the best performance.It is easy to oxidize, and is also conductive after oxidation)
How does it work?
Electroplating is the application of electrolytic cells in which a thin layer of metal is deposited onto an electrically conductive surface.
A cell consists of two electrodes (conductors), usually made of metal, which are held apart from one another. The electrodes are immersed in an electrolyte (a solution).
When an electric current is turned on, positive ions in the electrolyte move to the negatively charged electrode, called the cathode. Positive ions are atoms with one electron too few. When they reach the cathode, they combine with electrons and lose their positive charge.
At the same time, negatively charged ions move to the positive electrode, called the anode. Negatively charged ions are atoms with one electron too many. When they reach the positive anode, they transfer their electrons to it and lose their negative charge.
ELECTROPLATING PROCESS
The electroplating process is a method of using an electric current to dissolve metal and deposit it onto the metal surface. The process needs four primary components:
1) Anode: The anode, or positively charged electrode, in the circuit is the metal that will form the plating.
2) Cathode: The cathode in the electroplating circuit is the part that needs to be plated. It is also called the substrate. This part plays as the negatively charged electrode in the circuit.
3) Solution: The electrodepositing reaction takes place in an electrolytic solution. This solution contains one or more metal salts. Usually including copper sulfate, to help the flow of electricity.
4) Power source: Current is added to the circuit using a power source. This power source applies a current to the anode, introducing electricity to the system.
Once the anode and cathode are placed in solution and connected, the power supplies a direct current (DC) to the anode. This current causes the metal to oxidize. Allowing metal atoms to dissolve in the electrolyte solution as positive ions. Then the current causes the metal ions to move to the negatively charged substrate and deposit onto the piece in a thin layer of metal.
As an example, consider the process of plating gold onto metal jewelry. The gold plating metal is the anode in the circuit, while the metal jewelry is the cathode. Both are placed in solution and DC power is supplied to the gold, which dissolves in solution. The dissolved gold atoms then adhere to the surface of the base metal jewelry, creating a gold coating.
This process is constant. But there are three factors can impact the quality of the plating. These factors are below:
1) Bath conditions. Both the temperature and the chemical composition of the bath impact how effective the electroplating process is.
2) Part placement. The distance the dissolved metal needs to travel will affect how effectively the substrate is plated. So the position of the anode relative to the cathode is important.
3) Electrical current. The voltage level and the electrical current play a role in the efficacy of the electroplating process.
Material requirements
1–Most of the coating is a single metal or alloy. For example, titanium palladium, zinc, cadmium, gold or brass, bronze, etc.
2—There are dispersion layers, such as nickel-silicon carbide, nickel-fluorinated graphite.
3—There are cladding layers, such as a copper-nickel-chromium layer on steel, a silver-indium layer on steel, and the like.
4—In addition to iron-based cast iron, steel and stainless steel, electroplated base materials are non-ferrous metals, ABS plastics, polypropylene, polysulfone and phenolic plastics. However, plastics must undergo special activation and sensitization before plating.
we are a full-service electroplating and metal finishing provider. Our process capabilities include Chrome, Nickel, Zink-Nickel, Cadmium, Copper, Zinc, Tin-zinc, Zinc-iron, Electroless Nickel plating, Anodizing, Chem-Film, Passivation, Phosphate and Electro-polishing which are for products made of carbon steel, stainless steel, aluminum alloy, and super alloys. In addition, we offer non-electrolytic coating services. We serve renowned customers mainly in the automotive, aerospace, high-speed rail, energy, superconductor, and medical industries.
If you have investment castings need electroplating process,kindly contact us freely.