The pump housing isolates the pumped fluid medium from the atmosphere to prevent leakage and maintain pressure. For centrifugal pumps, the requirements for the pump casing are relatively high. For example, the sealing of the pump casing should be good, and the pump casing should have sufficient strength and rigidity. The flow channels of the pump body and the pump cover should be kept clean after casting. Each type of pump housing is designed according to the application requirements. It can meet the application environment of the pump. As a foundry of pump housings, we have cast many different pump housing types. This article will cover the types of lower pump housings.
Classification according to the inlet and outlet position
Positive displacement pumps surround a rotating or reciprocating displacement element (eg one or more pistons). The inlet and outlet are used to direct the pumped fluid in and out of the pump housing. It is usually divided into suction nozzles and discharge nozzles according to their functions. They can be directly connected to the system piping by means of flanges, pipe joints, and welding. It can also be done in the following two ways. Their pump housing types are different too.
Shell pump: The suction nozzle is immersed in the open liquid supply pool and tank. An example is a vertical shell pump with an axial propeller.
Invasive pumps: Two nozzles are immersed in the fluid along with the entire pump housing. Such as immersion submersibles, and sewage pumps.
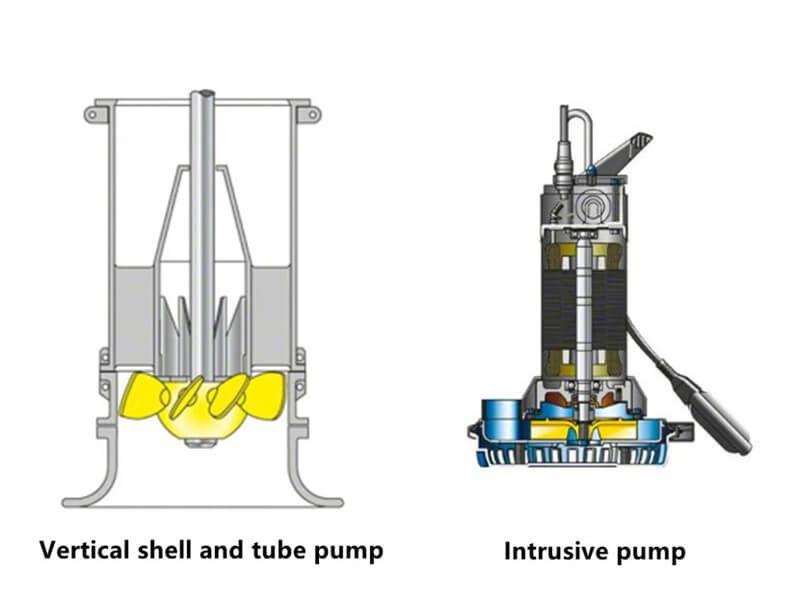
According to the shell shape
Each type of pump will have a different pump housing type. The shape of the pump housing is related to the specific speed. Shells of different shapes can be divided into the following types.
1) Volute-shaped housing. The shell of this shape can be divided into single volute and double volute. The double volute structure consists of two volutes offset by 180° to balance radial forces.
2) Vortex housing (vortex volute). The cross-section of the vortex casing is clearly asymmetrical on the meridian plane, reference can be made to the volute pump with mixed flow impeller and vortex volute.
3) Ring housing (ring housing). The circumference of the annular casing has a constant cross-sectional area. Which can be referred to as a double-suction annular casing pump.
4) Elbow housing. Elbow housing input flow is discharged into the elbow (housing) through a diffuser, see Elbow Housing Pumps.
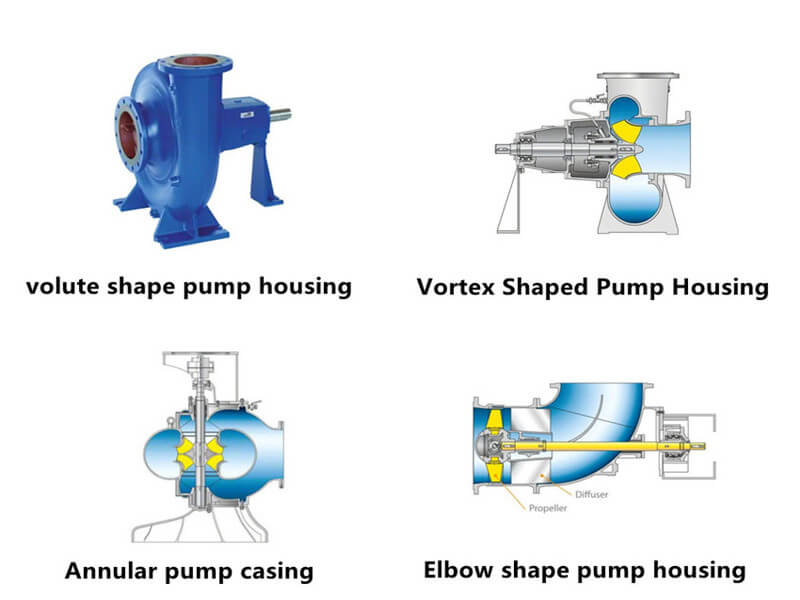
According to the pressure range
The pressure range also has an effect on the pump housing. So, the design of some pump casings will be designed according to the pressure of the conveyed fluid.
Housings for low-pressure pumps need different housing designs than those used for high- and ultra-high-pressure pumps. Increasing the pressure rating requires increasing the wall thickness of the pump casing. But, the dimensions of the pump housing must follow international codes and standards.
For high-pressure volute pumps and multi-stage high-pressure pumps, their housing geometry is designed as cylindrical (barrel core pump), conical or spherical (circulating pump). Such as a barrel boiler feed pump. Circulation pump with spherical casing.
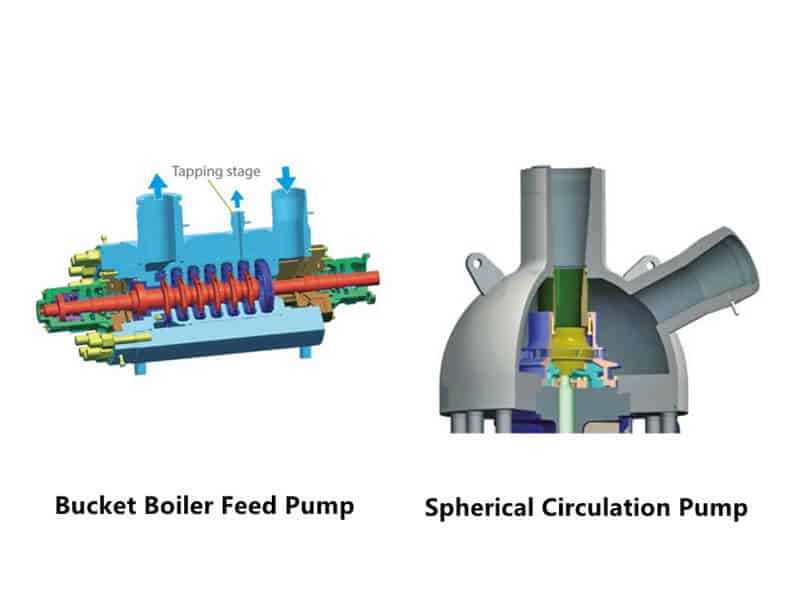
Although the internal pressure of the pump is higher. But these designs cut stress on the pump casing. Also, it can be adapted to the manufacturing method used in the production of thick-walled parts.
A vertical barrel pump is a different type of pump than a barrel-type core pump or barrel-type casing pump. Its suction characteristics make it widely used in condensate pumps or refinery pumps. The suction of the pump is enclosed by its outer barrel.
According to the structure
Sometimes the disassembly and structure of the pump is also a reference factor in the design of the pump casing. According to these reference factors, the pump casing can be designed in both radial and axial split configurations with respect to the shaft. For example, the radially split vertical volute casing pump and the axially split horizontal double-suction (volute casing) pump are designed for pipelines.
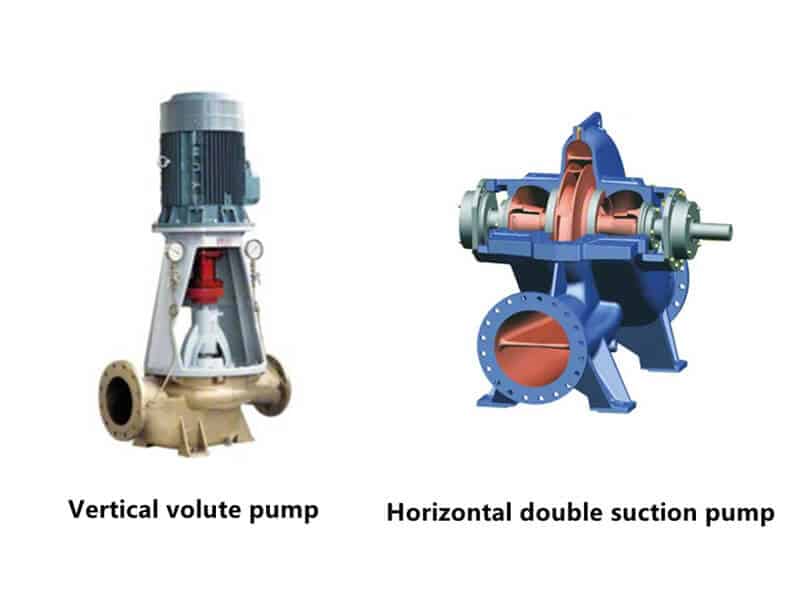
According to the position of the nozzle
The shape of the casing of the pump is also designed according to the position of the nozzle of the pump. for example1 In-line pump with nozzles arranged opposite each other.2 Refinery pump with “jack in jack out” orifice.3 Volute casing pumps with axial inlet pipe (end suction).
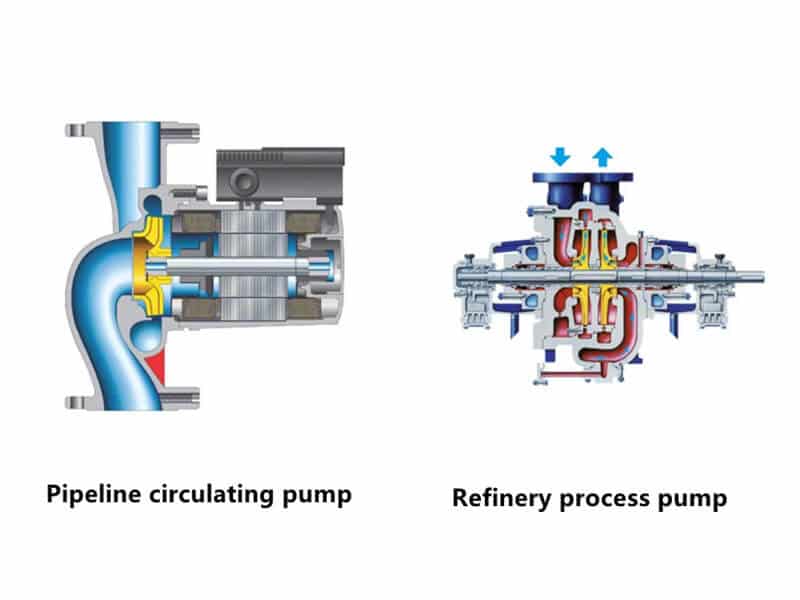
According to the pump function
The housing parts of the segmental pump are named according to their function. Such as suction casing, interstage casing and discharge casing. Examples are segment pumps with product lubricated bearings and segment boiler feed pumps.
When the segmented pump is assembled, the tight connection of the casing is ensured by connecting bolts/through rods. Gaskets and O-rings are mostly passed between the shells. Or resist internal pressure with direct metal-to-metal sealing.
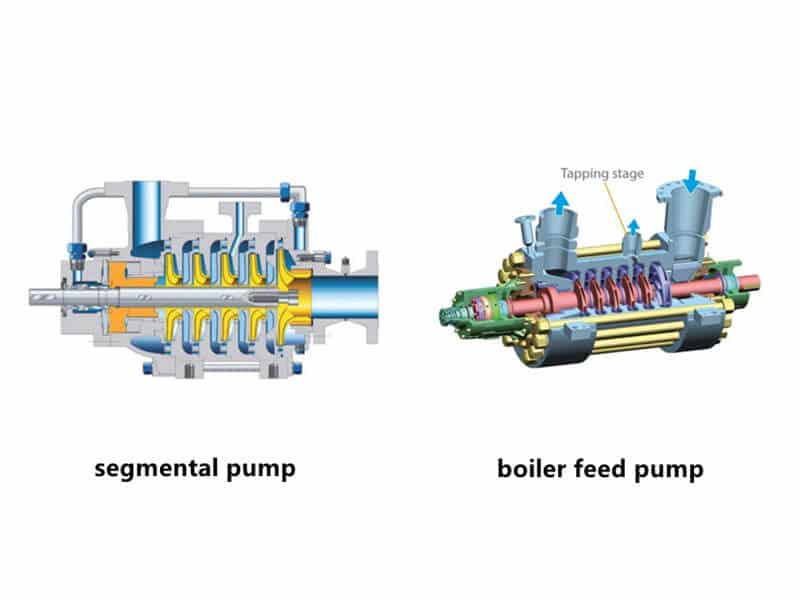
According to the manufacturing method and material of the pump casing.
The main manufacturing methods of the pump casing include casting, forging, welding, stamping, and cold drawing. Casting is the most common method of manufacturing pump housings.
The safe operation of the pump depends largely on the durability of the pump housing. Many industry-specific pumps have incompatible pump housing materials and specifications. In some cases the wall thickness of the pump is also specified.
Our common pump casting method can use many metals as materials. Including cast iron, ductile iron, cast steel, martensitic stainless steel, austenitic stainless steel. Also includes duplex stainless steels for highly corrosion-resistant materials (eg desalination applications).
According to the flow of the pump
The pump housing of a high-flow single-stage vertical pump is usually made of concrete. For example, shell pumps for low-lift pumping stations. As shown in the figure used for low-lift pumping stations. Concrete volute cooling water pump for oversized volute pumps. As shown.
Other Categories.
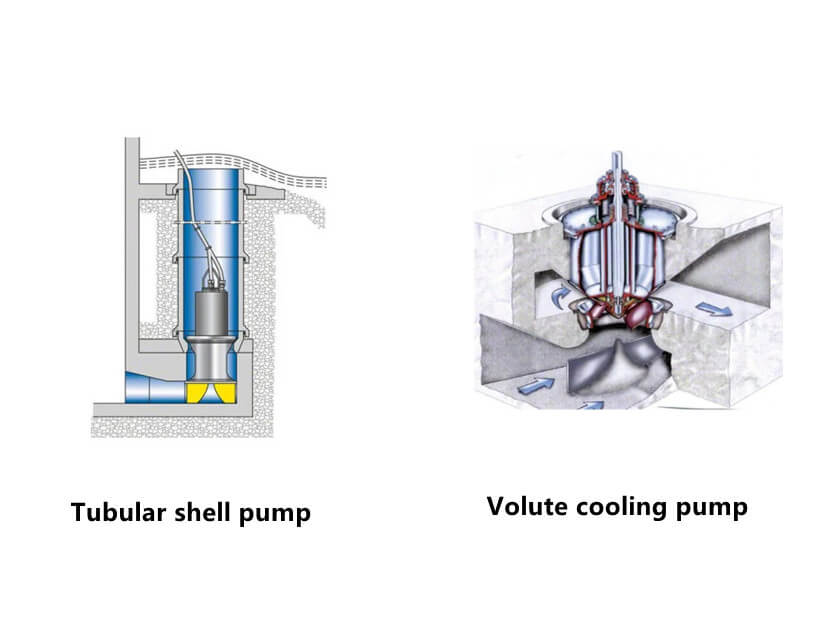
Other Types
The split pump can be divided into various types of pump casings.
For example, in the case of a horizontal pump, the casing of the pump is composed of upper and lower parts. The upper part of the pump housing has a simpler design. The lower part contains the pump inlet and outlet ports and pump feet. For example, a double-suction split volute pump.
The split pump casings are connected by flanges in the upper and lower casing halves. This flange extends over the entire pump housing. Includes two sealed stuffing boxes and is fastened (sealed) by many bolts. This withstands operating pressure and prevents leaks.
In addition to the housing types described above. The pump housing also sometimes includes a heat shield or cooling jacket, which is usually closed by a special cooling cover. Likewise, the pump housing sometimes includes a heating or insulating jacket. Their function is to keep the pumped medium at a certain temperature in the pump housing. Where the pump is not running by means of uninterrupted heating/insulation. To prevent it from precipitation, solidification or crystallization. For example, standard chemical pumps with heating jackets on the suction and discharge sides.
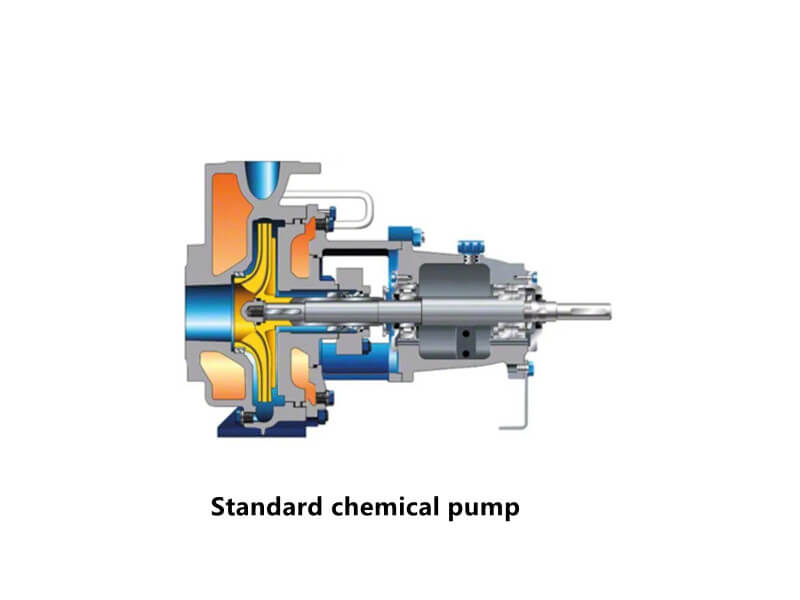
For all types of pump housings, we can produce them. We can customize the pump housing according to the parameters and material requirements. If you do not know how to choose the material of the pump housing, we will also provide you with the best solution.