With the development of modern casting technology, the casting process has led to a broad of different, specialized casting methods. Mainly there are 3 Different Types of Casting processes. They are Die casting, Investment casting, and Sand casting. Each of them provides its own unique fabrication benefits.
The casting manufacturing method is the process of pouring molten metal materials into a mold. After solidification, pick up the workpiece from the mold. To make a post finishing treatment or for use as a final finished product.
The Casting process can create a variety of parts that can be used in different industries. From daily life hardware, mechanical devices, construction supplies, automotive components to aerospace parts, electronics, medical products.
To know well both the advantages and disadvantages of types of the casting process. It can help us to select the suitable producing method for the desired product.
Sand Casting
Sand casting is one of the simplest types of casting with a long history. It is mainly used for producing large parts. It relies on silica-based materials. Such as naturally bonded sand, synthetic sand. It was been by filling a molten metal into the mold cavity that has been shaped from natural or synthetic sand. After cooling to get a workpiece.
The sand can be strengthened with the addition of clay. It helps the particles bond closely. Such as engine blocks and housings. Many automotive products are manufactured by sand casting processing. Compared to other mold casting processing, Sand casting is also suitable for smaller orders and can save cost.
Sand Casing Advantages VS Disadvantages
Advantages of Sand Casting | Disadvantages of Sand Casting |
A capacity for casting both ferrous and non-ferrous materials. | Large castings have a rough surface finish |
A low cost for post-casting tooling. | Close tolerances difficult to achieve |
The ability to fabricate large components. | Long, thin projections not practical |
Relatively inexpensive production costs, especially in low-volume runs. | Some alloys develop defects |
Usually limited to smaller parts than possible with green sand |
Sand Casting Process
Sand casting is a casting process that uses sand as a mold. Then pour the liquid metal into this mold to create a casting part. Its main process is as below:
sand preparation— mold making— core making—modeling—pouring—sand falling- –grinding processing— inspection.
Image credit: https://en.wikipedia.org
For its processing step details, kindly check the article of What is Sand Casting?
Sand Casting Applications
- Cylinder head.
- Automotive engine block.
- Crankshaft,and so on.
Sand Casting Products
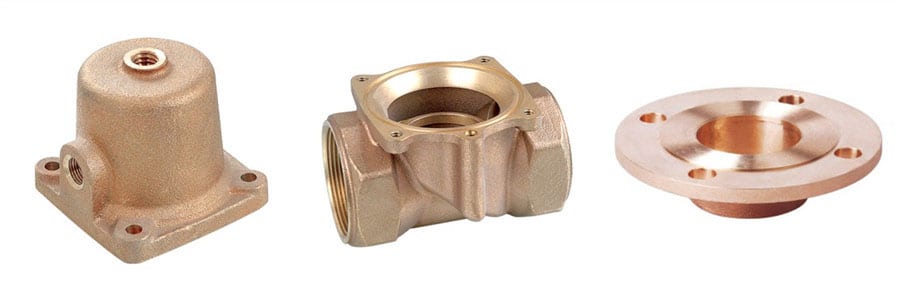
Investment casting
Investment casting (also known as lost wax casting) is a casting process that has been practiced for thousands of years. The lost wax process is one of the oldest known metal-forming techniques.
It is usually used for difficult manufacture, with a special form of parts that cannot be formed by usual manufacturing techniques.
Like turbine blades or components of airplanes. Compared to other casting processes, such as die-casting or sand casting, it is an expensive casting process.
But it can produce intricate contours casting parts. In most cases, the components are cast near the net shape.
Advantages of Investment casting vs Investment casting Disadvantages
Advantages | Disadvantages |
A high degree of accuracy and precise dimensional results. | Size of part limited |
The ability to create thin-walled parts with complex geometries. | Expensive Cost |
The capacity for casting both ferrous and non-ferrous materials. | Patterns and molds |
Relatively high-quality surface finish and detail in final components. | High labor costs |
Investment casting Process
Use wax or plastic to make a pattern. Then coat refectory to be a shell. Then heat the shell to melt the wax to get a hollow cavity. Then pour the melted metal to be casting.
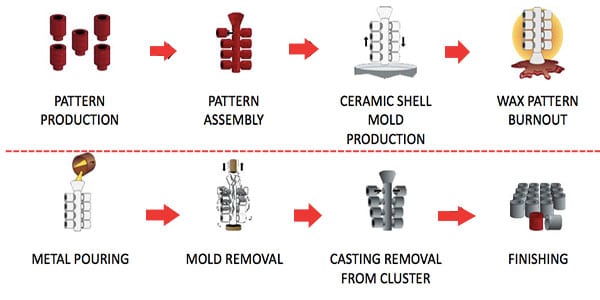
Investment casting Applications
- Small parts with complex shapes.
- High precision requirements.
- Or other processing that is difficult to perform. such as turbine engine blades.
Investment Casting Products
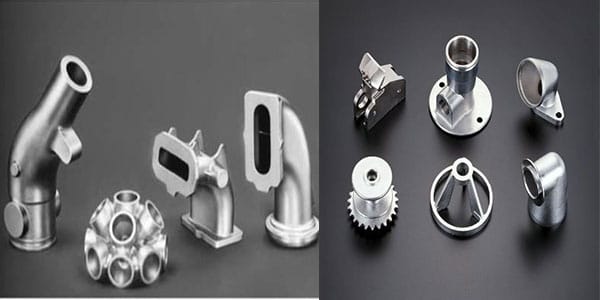
To know more details about investment casting, kindly view what is Investment Casting?
Die casting
Die casting is the process of molding materials under pressure. Generally, die casting is used in forming iron, aluminum, magnesium, and copper-based alloys and non-ferrous metals. It is characterized by the use of a mold cavity to apply high pressure to the molten metal. Molds are usually machined from higher-strength alloys. This process is somewhat like injection molding. For die casting, a cold chamber or a hot chamber die casting machine is required.
Casting equipment and molds costs are expensive. So, die casting processes are generally used to mass-produce a large number of products. It is relatively easy to make die-cast parts.
This generally requires only four main steps. The cost per item is very low. Die casting is particularly suitable for the manufacture of large quantities of small and medium-sized castings. Die casting is the most used of all casting processes. Compared to other casting techniques, the die-cast surface is flatter. It has higher dimensional consistency.
Die Casting Process
At a high speed, the high-pressure metal liquid is pressed into a precision metal mold cavity. Waiting for the metal liquid to be cooled and to be a casting.
Die Casting Advantages VS Die Casting Disadvantages
Advantages | Disadvantages |
Close size and shape tolerances. | High initial die costs |
High component dimensional consistency and uniform design. | Limited to nonferrous metals |
A reduced need for post-casting machining. | Size of part limited |
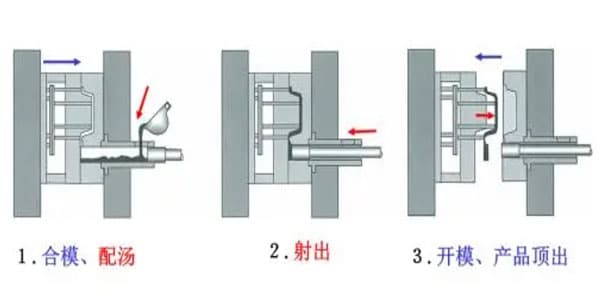
Die casting has 3 different types: Gravity Die Casting. Low pressure die casting. (LPDC) and High pressure die casting. (PDC)
Die Casting Applications
- Automotive industry and the instrument industry.
- Agricultural machinery.
- Machine tool industry.
- Electronics industry.
- Medical equipment,
- Clocks.
- Daily hardware.
Die Casting Products
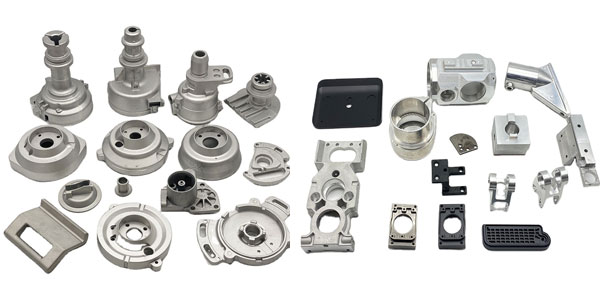
To know more details about die casting, kindly view What is Die Casting?
China Casting Foundry
JC Casting is a leading casting manufacturer in China. With 20+ years of history, we have serviced many customers from all over the world. They are from different industries. Their product producing methods need more and different types of Casting processes.
Our engineering and technical team has great experience in the casting industry. They can give you a good and save-costing solution as per your need. Kindly contact us, you will get a satisfactory answer.