In this article, we will be focusing on them and compare Investment casting vs die casting.
Casting is one of the oldest and most traditional manufacturing methods for parts. Although there are now several types of casting methods. They all still have the same fundamental of casting liquid material is poured into and hardened.
Investment casting and die casting are two of the most popular casting methods. The investment casting method is to inject wax into an aluminum cavity. Die casting is the process in which molten metal is forced into a mold cavity with high pressure.
Although the castings from both methods seem similar, they take a very different process to create a cast. In this article, we will be focusing on them and compare Investment casting vs die casting. How are they different, their own advantages and disadvantages? What different kinds of products are used to? What should you consider when choosing between the two? Which one is better for your choosing?
What is Investment Casting
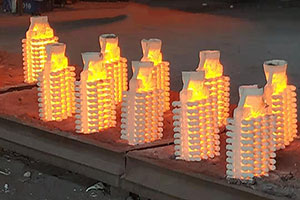
Investment casting seems like a more high-grade casting method. But it has also appeared since ancient times. The investment casting process has more steps and is more complex.
Its main process steps are as below:
- 1-Investment casting manufacturers use a product wax pattern to make a mold.
- 2-Then they dip the wax pattern into a refractory slurry. To made of materials like plaster of silica or sillimanite and silica to form the mold.
- 3-After dipping the wax into the slurry, manufacturers heat the pattern to melt and remove the wax. 4-After harden the slurry binders. They then pour molten metal into the mold and allow it to cool.
- 5-The mold or pattern of investment casting is made of aluminum or steel. Then dipping the tree assembly into the refractory slurry to form a ceramic shell.
- 6-Finally pouring molten metal into the shell by the pouring gate and cooling for solid casting blanks.
The investment casting process is more complex. However, its surface finishing and having tighter dimensional tolerances.
Advantages and Disadvantages of Investment Casting
Advantages of Investment casting | Disadvantages of Investment casting |
Cast ferrous and non-ferrous materials | Expensive Cost than sand casting |
Smooth surface finishes, reducing machining and finishing | Longer Lead time |
Investment casting in thin-walled parts with complex shapes | |
Very accurate, Create products with precise dimensions even net shape |
What is die casting?
Die casting is the more old-fashioned metal casting process. It is characterized by the use of a mold cavity to apply high pressure to the molten metal. Molds are usually machined from higher-strength alloys. To understand the die casting process easily, let us break it down into two steps:
1) MOLD making.
The die casting mold is typically machined from a block of hardened steel or high-strength alloy. This process speeds up the turnaround time for the mold cavity.
2) POURING.
Pouring the molten metal into the cavity at high pressure. After cooling and solidifying, it is ejected from the mold and the process is repeated.
Most die castings are iron-free. For example zinc, copper, aluminum, magnesium, lead, tin, and lead-tin alloys and alloys.
As per the type of die casting, a cold chamber dies casting machine or a hot chamber die casting machine is required.
Casting equipment and molds costs are expensive. So the die casting process is generally only used to mass-produce a large number of products. That makes the cost per item is very low.
Advantages and Disadvantages of Die Casting
Advantages of Die Casting | Disadvantages of Die Casting |
Good product quality | Castings are prone to generate air holes and cannot be heat treated |
High productivity | Die casting is difficult for complex concave castings |
Excellent economic effect | High melting point alloys (such as copper, ferrous metals), die casting type has a shorter life |
Not suitable for small batch production. Because of high manufacturing cost |
Investment Casting vs Die Casting

Investment Casting is a metal thermal processing process. Die casting is one of them. The main differences between of them are as follows:
1–Definition different
Casting is a metal thermal processing process. The liquid metal is cast into a casting cavity adapted to the shape of the part. And after cooling and solidifying, a method of obtaining a part or a blank. Die casting is a metal casting process. It is a precision casting method that uses high pressure to force the metal to be hydraulically poured into a complex metal mold.
2–Material Selection different
The investment Casting process allows for both ferrous and nonferrous alloys. It has more range of material selections. Die casting is mainly adapted for materials like aluminum, zinc, and magnesium alloys.
3–Characteristics different
A common feature of investment casting is heat treatment. The high pressure and high-speed filling die casting are the two characteristics of die casting.
4 –Cost different:
Investment casting is a highly manual working process. And it can produce superior dimensions and a good surface finish. So it seems like a high-cost casting method. But it is also the most possible technique to reduce or avoid secondary machining. So that reduces the time and money.
Die casting costs are more because of its high tooling cost and post-machining requirements. So for large and mass order quantities, die casting is more cost-effective.
5–Surface treatment is different:
In all casting techniques, the investment casting surface finish is always the best. As standard, it can reach precise tolerance IT5-6 with A 125 micro finish.
Although die casting can also create a good surface finish, it needs more machining to get the final result.
During actual production, we can both improve the surface finish of investment casting and die casting by secondary machining and other surface treatment ways.
6–Design and size
Investment casting offers greater design flexibility. It can achieve precise dimensions, complex geometries, and thin-walled parts. But its size and weight are limited. In our factory, we can make investment castings up to weight 100kgs.
Die Casting has and can create larger components. For larger products and lower quantity orders, its unit cost and tooling cost are higher.
Which method should you choose?
Die casting and investment casting are both commercially valuable methods for manufacturing. Especially for high-strength steel or metal parts. But, they are different enough from each other. So to decide which method is better for your situation is more beneficial.
When you choose to die casting
- 1–You need a volume of orders
The mold cost for die casting is too expensive and takes a lot of work. But, this mold using life can reach up to a million produced parts.
If your order’s quantity can be at this magnitude, the unit cost per piece of die-casting becomes very low.
- 2–You need quick turnaround times
Once the die casting mold was ready, the part production and output becomes a simple and repetitive process.
It is perfectly suitable for automation, such as in JC casting. Now, a large-scale die casting facility is still very common. And its production effect is also fast for finished parts.
- 3–You need large parts
Die casting products size is larger than investment castings. Although it needs more complex and expensive machining, it is possible to make any part size with die casting. This is not easy for investment casting. It has to consider the wax lost technic and pouring process request.
When you choose investment casting
- 1–You need net shape products
Design freedom and strict tolerance are the core areas of investment casting excels. When you’re working with a wax master pattern, it is easy to incorporate subtle design elements. If you need to recreate a model with complex patterns and net shape features. It is the best choice to go into investment casting.
- 2–When you need ferrous and non-ferrous metals
The die casting limitation is that its mold cannot be exposed to temperatures higher than the melting point of the mold material. This limits the materials for die casting are mainly non-ferrous metals.
But Investment casting has no such restrictions. The refractory materials of investment casting can be both ferrous and non-ferrous materials.
Conclusion
Die casting and investment casting are both well-established casting methods. One is better for large-scale production. The other is better for producing at a lower scale. They also have good and bad points for each option. So the choice is depended on your product’s requirements.
If the material is steel or iron, a small product with a complex shape, Investment casting is the best choice. If the huge quantity and the material is aluminum or zinc, die casting will be your right option.
After learning the Investment Casting vs Die Casting, hope it is useful for you. If you have any inquiries about Investment Casting and Die Casting, contact us freely. you will get an immediate reply within 12 hours.