As one of the investment casting companies in china, we produce a variety of precision components with different Investment Casting Materials. The investment casting process is complex processing. We have to consider the final products functions, materials cost-saving, precision casting defects, and limit the secondary processes after the casting. Final parts can display smooth surfaces and dimensional precision while allowing for lower weight, thin walls, or other beneficial properties. The casting part properties can be successfully incorporated into or not is largely depends on material choice.
So how to choose the correct investment casting materials is becoming more and more important. Today, let’s learn about the Investment Casting Materials different. What are materials suitable for investment casting?
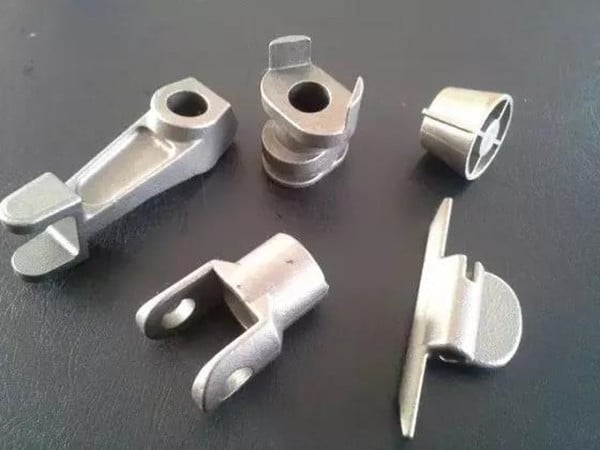
Investment Casting Materials types List
There is a large choice of Investment Casting Materials types for investment casing. It includes:
Stainless Steel | Cast Aluminum | Aluminum Alloy |
Carbon Steel | Cast Iron | Brass and Bronze |
Copper Alloy |
Stainless Steel
Stainless steels feature superior durability in comparison with many other materials. The potential of the material has led to increased use in investment casting by designers and engineers. Applications for stainless steel: gearbox parts in automotive applications, various gears, camp components, and golf club heads.
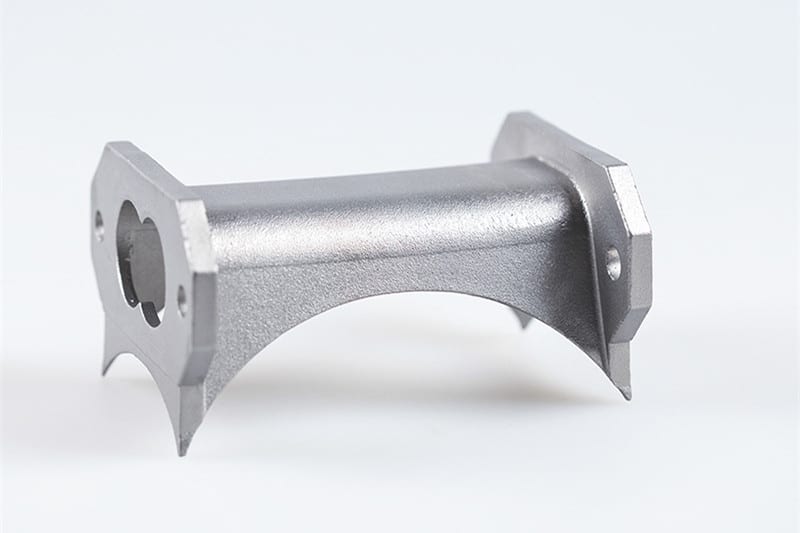
Steel alloy
A steel alloy with a minimum of 10.5% chromium content by mass, stainless steel is highly corrosion resistant and wear-resistant, provides excellent machinability, and is well-known for its aesthetic appearance. As one of the industry’s leading stainless steel casting companies, we design and manufacture a wide range of custom stainless steel parts, such as • Ball valve components • Steam trap components • Poultry processing components • Complete hinge assemblies • Parts for agricultural implements
Low Alloy Steel
Low alloy steels are among the most frequently used steels in the mechanical world due to their affordability and beneficial mechanical properties. Specialized heat-treating processes make it possible to engineer parts that have different properties in different areas of the same workpiece. For example, varying heat treatments can be used to make one surface tough and impact-resistant, while another surface becomes wear-resistant.
Cast Aluminum
Common cast aluminum grades: ADC-12, A356, A380, ZL104.
In addition to cookware and furniture, this type of investment casting material is also used to create several motor parts for land vehicles and boats. Components such as connecting rods, pistons, housings, radiator tanks, and other essentials can be created using both die casting and mold casting methods. Even components such as compressors and various types of gears may be created using aluminum of this type. Cast aluminum is a specific metal that has gone through one of the several processes known as casting. Essentially, it is created when methods such as die-casting, mold casting, or sand casting are used to temper the aluminum for use in creating components for many different types of products. This form of aluminum is used for some items around the house, as well as machinery and other products that are necessary to the manufacturing of a wide range of goods and services.
One of the main advantages of using cast aluminum is that the metal is often cost-efficient in comparison to other investment casting materials. The metal also retains a high degree of durability. While it is not necessarily true that it will last as long as cast iron in some applications, aluminum products do tend to hold up well for some years. The combination of lower cost and reliable durability makes the metal an excellent choice for many aluminum castings used in domestic and commercial applications.
Aluminum Alloy
Aluminum Well-known for its high strength-to-weight ratio, aluminum can be heat treated to achieve greater strength, ductility, corrosion resistance, and machinability. During aluminum investment casting, we use resistance melting and extensive de-gassing methods to pour aluminum in NDT levels up to Class 1, Grade A (Grade B for production) to produce components like • Heat Sinks • Valves • Medical Devices • Levers • Pistol Frames
Aluminum alloy is the most used material in investment casting. Industries that use it most frequently include aerospace, avionics, electronics, and the military.
Castings are now offered for demanding applications like airframe components thanks to the material’s improved strength and the availability of quality castings made from aluminum-silicon-magnesium alloy.
Carbon Steel
Carbon steel is a common low-cost material that comes in a variety of grades, with the classifications varying based on the amount of carbon content. The strength, ductility, and performance of carbon steel can be improved in industrial applications through heat treatment. Its ferromagnetic properties make carbon steel useful in motors and electrical appliances. It is safe, durable, and has high structural integrity, making it one of the world’s most frequently used alloys.
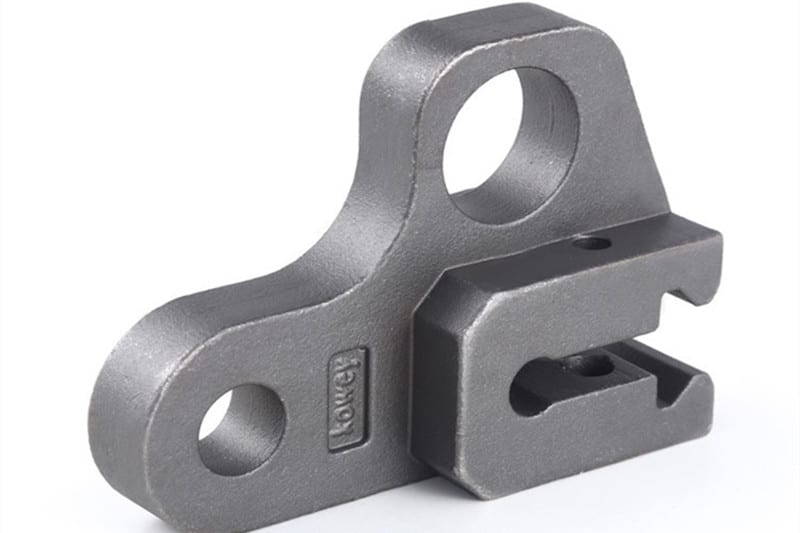
A popular material for a wide range of applications, carbon steel is inexpensive, readily available in numerous grades, and can be heat-treated to improve its strength, ductility, and machinability. We pour a variety of alloys to create custom carbon steel investment-casted components including • Door locks and internal lock mechanisms • Gun triggers, hammers, and sights • Critical parts for the mining and transportation industries, among others
Super Alloy
Superalloys based in nickel and cobalt have common uses in the aerospace, energy, medical, chemical, and marine industries. Nickel-based alloys are stronger at high temperatures and cobalt-based alloys have superior corrosion, oxidation, and wear resistance over their nickel-based counterparts. Superalloys increasingly replace sheet metal because they provide high rigidity and superior service characteristics while remaining a cost-effective option.
Cast Iron
Iron castings, which often include gray iron and ductile iron, are known for their high accuracy and an affordable price tag. Ductile iron has high strength, heat resistance, and toughness, but it has a more complex production process than other steels. This leads to a higher production cost than cast steel.
Cast iron usually refers to gray iron and ductile iron. Such kind of investment casting material can be used to produce iron castings with carbon content higher than 2%.
Common gray iron grades: HT150, HT200, HT250, HT300, HT350.
Common ductile iron grades: QT400-15, QT400-18, QT450-10, QT500-7, QT600-9.
Copper Alloy
Copper-based alloys are corrosion-resistant and feature low rates of wear. They are frequently used in applications such as ship or pump propellers, electrical components, and plumbing components. A versatile material, more than 400 different alloys are featuring a wide variety of properties.
Many part types can be investment cast from copper-based alloys. More common types of copper-based alloys include bronze and brass. The strongest copper alloy is beryllium-copper, which has similar properties to high-strength alloy steels but with a higher corrosion resistance over longer periods.
Brass and Bronze
Brass and Bronze Both brass and bronze exhibit excellent machinability and corrosion resistance, are non-sparking, lack magnetism, and provide unique wear characteristics and aesthetics. We provide tight tolerances and exceptional part-to-part repeatability for brass and bronze investment-casted parts, including • Impellers • Door handles and complete hinge assemblies • Pump components
Special Alloys
Pouring more specialty alloys than any other investment casting company in the industry today, we manufacture components for the fluid power, oil and gas, marine technology, food and dairy, and aerospace industries among others, using a wide range of alloys, including • Inconel • Monel • Chrome-cast iron • Hastelloy • Cobalt • Nitronic® 50 • Copper • “Beryllium Copper” • Duplex stainless 2205 • Tool Steel
Investment Casting from us
Investment casting materials have different properties and uses, which is why it is important to choose the correct casting material for your application. Proper material selection will ultimately help you achieve the desired functionality of your design. It can cut costs and material waste. For more information on material selection, or to learn about our investment casting services.