Heat treatment is of great significance to cast or forged workpieces. It can change the product’s internal structure and improve its performance. There are four basic processes for heat treatment. They are Normalizing, Tempering, Annealing, and Quenching. Today, let’s have a brief view of them.
Quenching
1–What is Quenching?
Quenching refers to a metal heat treatment process. In the processing, the metal workpiece is heated to an appropriate temperature and maintained for a period of time. Then immersed in a quenching medium for rapid cooling.
Strictly speaking, Quenching is to heat the steel to the critical temperature Ac3 (hypo-eutectoid steel) or Ac1 (hypo-eutectoid steel). Then keep it for a period of time to make it completely or partially austenitized. Then the steel is quickly cooled. Cooling below Ms (or isothermally close to Ms).
Quench hardening is a mechanical process. In this process, the workpiece strengthened and hardened. These metals include ferrous metals and alloys, steel and cast iron alloys.
The material is then usually tempered to reduce the brittleness that may increase due to the quench hardening process. Products that can be quenched include gears, shafts and wear blocks.
Besides, the solution treatment of aluminum alloy, copper alloy, titanium alloy, tempered glass and other materials. Or the heat treatment process using a rapid cooling process is also called quenching.
2–What is the purpose of Quenching?
1) Improve the mechanical properties of metal materials or parts. Such as hardness, wear resistance, elastic limit, fatigue strength, etc.
For example:
- Improve the hardness and wear resistance of tools, bearings, etc.
- Improve the elastic limit of springs.
- Improve the comprehensive mechanical properties of shaft parts.
2) Improve the material properties or chemical properties of special steel.
For example:
- Improving the corrosion resistance of stainless steel.
- Increasing the permanent magnetism of magnetic steel.
3) The quenching process should also ensure the processed part size and geometric shape changes. to ensure the accuracy of the parts.
Tempering
1-What is Tempering?
Tempering is a heat treatment process in which the quenched metal material or part is heated to a certain temperature. Then keep warming for a certain period of time. Then cooling in a certain way.
Tempering is usually made after quenching. It is rapid cooling of the metal to put it in its hardest state. It is usually the last step of the workpiece heat treatment. The combined process of quenching and tempering is called final treatment.
Tempering is applied to alloys. Such as steel or cast iron, to achieve greater toughness by decreasing the hardness of the alloy. The reduction in hardness is usually accompanied by an increase in ductility, thereby decreasing the brittleness of the metal.
2–What is the purpose of Tempering?
1) Reduce internal stress and reduce brittleness. Quenched parts have great stress and brittleness. If they are not tempered in time, they will tend to deform or even crack.
2) Adjust the mechanical properties of the workpiece. After quenching, the workpiece has high hardness and high brittleness. To meet the different performance requirements of various workpieces. it can be adjusted by tempering, hardness, strength, plasticity and toughness.
3) Stabilize the size of the workpiece. The metallographic structure can be stabilized by tempering. This can ensure no deformation occurs during use.
4) Improve the cutting performance of some alloy steels.
Normalizing
1–What is Normalizing?
Normalizing is a heat treatment that improves the toughness of steel. It is to heat the workpiece to a suitable temperature and then cool it in the air. Strictly speaking, Normalizing is heat the steel component to 30-50℃ above the Ac3 temperature, keep it for a period of time. Then it is air-cooled. The main feature is that the cooling rate is faster than annealing and slower than quenching.
The effect of normalizing is like annealing. The material’s structure becomes finer. It is often used to improve the cutting performance of materials. Sometimes, it is the final heat treatment for parts that are not demanding.
During the normalizing process, the grains of steel can be refined in slightly faster cooling. Not only can satisfactory strength be obtained, but also the toughness (AKV value) can be significantly improved. The tendency of components to crack is reduced.
After normalizing, some low-alloy hot-rolled steel plates, low-alloy steel forgings, and castings, the comprehensive mechanical properties of the material can be greatly improved. At the same time, the cutting performance is also improved.
2–What is the purpose of Normalizing?
1) It can eliminate the overheated coarse-grained structure of casting, forging, and welding parts. Band structure in rolled material. It can be used as a pre-heat treatment before quenching.
2) It can eliminate the net-like secondary cementite. Make the pearlite refinement. Not only improve the mechanical properties but also help the next spheroidizing annealing.
3) It can eliminate the free cementite in the grain boundary to improve its deep drawing performance.
Annealing
1–What is Annealing?
Annealing is a metal heat treatment process that slowly heats the metal to a certain temperature. Then keeps it for enough time, and then cools it at an appropriate speed. The purpose is to make the internal structure of the metal reach or close to the equilibrium state. Good process performance and use performance. Or prepare the structure for further quenching.
Annealing is divided into complete annealing, incomplete annealing, and stress relief annealing.
2–What is the purpose of Annealing?
1) Improve or eliminate various structural defects and residual stresses caused by steel casting, forging, rolling, and welding, and prevent deformation and cracking of the workpiece
2) Soften the workpiece for cutting
3) Refine the grains and improve the structure to improve the mechanical properties of the workpiece
4) Prepare the organization for the final heat treatment (quenching, tempering)
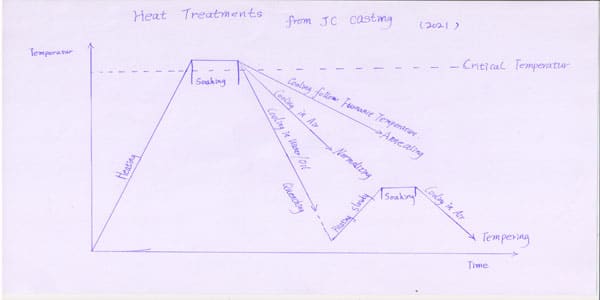
Difference between normalizing, tempering, annealing and quenching
The difference between normalizing, tempering, annealing and quenching is that the process is different, the material structure changes, and the material properties change results.
1. Process different:
Normalizing is to heat the workpiece to Ac3. (Ac is the final temperature at which free ferrite is converted to austenite during heating. Generally, it is between 727 °C and 912 °C) or Acm (Acm is over-eutectoid in actual heating). The critical temperature line for complete austenitization of steel) is above 30~50 °C. After holding for a period of time, then taken out from the furnace.
It is a metal heat treatment process of spraying water, spraying, or blowing air in the air.
Tempering treatment means that the quenched or normalized steel is cooled at a certain rate after being immersed for a period of time below a critical temperature.
Annealing is a metal heat-treatment process. it heats the metal to a temperature for enough period of time. Then cools it at a suitable rate (usually slow cooling, sometimes controlled cooling).
Quenching is the heating of steel to a temperature above the critical temperature of Ac3 (hypoeutectic steel) or Ac1 (hyper-eutectoid steel). Keep it for a period of time to make it all or part austenitized. Then, martensite (or bainite) transformation is performed by rapidly cooling to a temperature below the critical cooling rate to below Ms (or isothermal near Ms).
2. Material organization changes different.
The Material organization After normalizing. the sub-aluminum steel is ferrite + pearlite, the eutectoid steel is pearlite. The hypereutectoid steel is pearlite + secondary cementite. it is discontinuous.
Low-temperature tempering results in martensite structure. The tissue obtained by medium temperature tempering is tempered tortoise. The high-temperature tempering and quenching treatment results in a tempered sorbate structure.
After annealing, the grains are refined. the structure is adjusted, and the tissue defects are eliminated.
Quenching causes the supercooled austenite to undergo martensite or bainite transformation. A martensite or bainite structure is obtained. Finally, an unbalanced structure dominated by martensite is obtained. it is also having bainite or maintaining single-phase austenite as needed.
3. Material performance changes are different:
In the case of normalizing, the crystal grains of the steel can be refined in slightly faster cooling. Not only does it achieve satisfactory strength, but it also significantly improves toughness (AKV value). Reduce the tendency of the member to crack. Some low-alloy hot-rolled steel sheets, low-alloy steel forgings and castings, after normalizing treatment, the comprehensive mechanical properties of the material can be greatly improved. It also improves the cutting performance.
After tempering, it will be quenched and normalized and placed in the intermediate temperature for a period of time (aging) to promote the precipitation of a part of the carbide. At the same time, it can drop some residual stress caused by rapid cooling. So, the toughness and flexibility of the material can be improved.
Annealing can reduce the hardness. Improve machinability. Eliminate residual stresses. Stable size and reduced tendency to crack and crack. Refine grains, adjust tissue, and eliminate tissue defects. Uniform material organization and composition, improve material properties or prepare tissue for future heat treatment.
Quenching can greatly improve rigidity, hardness. wear resistance, fatigue strength, and toughness of steel. Thus to meet the different use requirements of various mechanical parts and tools. Special physical and chemical properties ( such as ferromagnetism and corrosion resistance of certain special steels) can also be met by quenching.
4.Annealing, normalizing, quenching, tempering sequenceIn
The four processes of heat treatment, quenching and tempering are used in combination. There is no fixed order. The process needs to be tailored to the specific situation. For example, normalizing can be used as a residual heat treatment or as a final heat treatment.
Below is a video for Annealing, normalizing, quenching, tempering
Example to explain the different between Annealing, normalizing, quenching, tempering
Heat treatment in the industrial field may be very abstract for beginners. Below I will use a metaphor to explain the difference between them!
Annealing. Slowly heat the metal to a certain temperature. Keep warm for a while. Then slowly cool to room temperature.
Think about it: you cooked the food but it was too hot. So you have to put it aside. Let it be cold and eat. Annealing is like this.
Normalizing. It is to heat the metal to 30-50 ° C above the critical temperature. The heat treatment process in which air is cooled after a suitable period of time. It sounds a lot like annealing.
Only the normalizing cooling rate is slightly faster and the production cycle is short. Because normalizing is like cooling down. It is often faster to eat, that is, to get products faster. So, when annealing and normalizing can also meet the performance requirements of parts. we can use normalizing as much as possible.
If annealing and normalizing are brothers, then quenching and tempering are good partners who will never leave.
Quenching. It is to heat the metal above the critical point. Now, the structure and state of the metal will change – austenitizing. We need to keep warm for a certain amount of time to let the metal make this change. It is then cooled at a temperature greater than the critical cooling rate. To get a metastable martensite structure or a lower bainite structure.
This method of rapid cooling is usually like this. After quenching, a martensite structure is obtained. But the internal structure of this organizational state is extremely unbalanced. Although the hardness is high, the plasticity and toughness are poor. It is also brittle. So, the quenched metal will not be shipped as a finished product. This product that cannot be reworked is like a mobile phone screen. For example, the mobile phone screen is fragile metal. No one will want it.
So, the role of tempering is reflected! After the metal is hardened, it is heated to a temperature below the critical temperature. Keep warm for a while. Allow the tissue inside the metal to be evenly distributed and then cool to room temperature. In this way, a finished product has a certain strength, hardness, and certain plasticity and toughness can be obtained.
This is the perfect example of 1+1>2!
If you feel this article is useful for you and the casting producer, welcome to share it with the public.
If you have any investment casting inquiries with heat treatments, kindly contact us freely.