Aluminum Investment Castings
As an aluminum casting supplier, We have our own aluminum investment castings foundry, We can offer aluminum die castings and aluminum investment castings. We have serviced many aluminum casting projects for our customers. such as from the USA, Canada, AU, Japan, Germany. UK.
Investment casting is one of the main processes for manufacturing aluminum components. We call this type of investment castings as aluminum investment casting. Why do we choose aluminum investment castings? Maybe the main reason is from its Advantages.
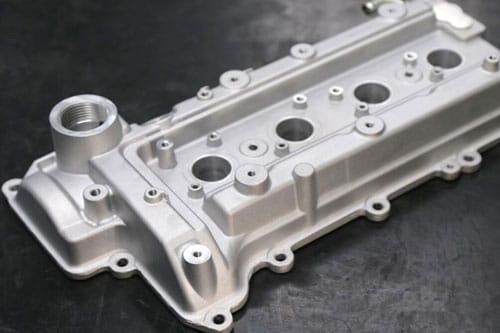
Advantages of Aluminum Investment Castings
1. Aluminum Investment Castings can allow the attainment of complex designs and forms. This means that manufacturers can easily order customized castings that will be suitable for their production needs.
2. Aluminum Investment castings allow producers to manufacture parts at an extremely higher and faster rate than other alloy materials. Aluminum die casting can also achieve near net shape so the process of machining can be eliminated to produce finished parts.
3. Aluminum investment castings have the strength of steel but very lightweight. The appearance and aesthetic value of aluminum parts are also superior to other metal alloys. However, aluminum die-cast parts are cheaper so end consumers can get high-quality metal products at very affordable prices.
4. Castings made from aluminum are versatile, corrosion-resistant, and can be used for different purposes. These qualities allow manufacturers to produce multiple products using aluminum parts. The finished products also have longer lifetimes thus giving consumers more value for their money.
5. Quantity flexibility. No matter the quantity is more or less, it can be produced at any time.
6. Has good thermal conductivity and heat dissipation. Therefore, it is widely applied to the radiator device.
7. Aluminum castings have a small specific gravity and a lightweight. Therefore, it is very popular among industries that require lightweight design such as aluminum car parts in automobiles, trains, and airplanes.
The above seven advantages make aluminum investment castings widely used. Especially in the mechanical equipment industry, automobile manufacturing industry, mining machinery industry. Aerospace industry and so on.
What is Aluminum?
Aluminum is an element. Its symbol is AL.
The density is 2.7 g/cm3.
The melting point is 660 ° C,
The boiling point is 2327 ° C.
Aluminum is a silver-white metal that is lightweight.
Has good ductility,
electrical conductivity,
thermal conductivity,
heat resistance
radiation resistance.
Aluminum forms a dense oxide film on its surface in air. Aluminum has good corrosion resistance. Our common aluminum products have been oxidized. Most of the alumina is silvery gray.
The content of aluminum in the earth’s crust is second only to oxygen and silicon. It is the most abundant metal element in the earth’s crust. It is often made in rods, sheets, foils, powders, ribbons and filaments in a wide range of important industrial fields. Such as aerospace, construction, automotive, and electric power.
The cast aluminum alloy is an alloy. It is filled with molten metal to obtain a blank of various shapes and parts. It has a low density and a high specific strength. Good corrosion resistance and casting process ability. Limited by the design of the part structure is small.
It is classified into Al-Si and Al-Si-Mg-Cu-based medium strength alloys. Al-Cu based high-strength alloy. Al-Mg based corrosion-resistant alloy. Al-Re based heat-strength alloy. Most products require heat treatment to achieve strengthening of the alloy, elimination of internal stresses in the casting, stabilization of the structure and size of the part.
It can be used in the manufacture of beams, gas turbine blades, pump bodies, pylons, hubs, air intakes and engine casings. It is also used in the manufacture of automotive cylinder heads, gearboxes and pistons, instrument housings and supercharger pump bodies.
The Aluminum Alloys we can supply.
A356 Aluminum Alloy
A356 is a 7Si-0.3 Mg alloy with 0.2 Fe (max) and 0.10 Zn (max). The T6 heat treatment is a solution-anneal heat treat followed by a 320F aging.
Alloy A356 has greater elongation, higher strength, and considerably higher ductility than Alloy 356. This type of aluminum alloy can be produced in both die casting and gravity casting.
Typical applications are airframe castings, machine parts, truck chassis parts, aircraft and missile components, and structural parts requiring high strength.
A360 Aluminum Alloy
A360 is harder to cast than A380, which is why many die casters avoid it. However, it does offer higher strength at high temperatures, better ductility, and higher corrosion resistance, so you may want to consider this alloy depending on your casting abilities and needs.
A380 Aluminum Alloy
The A380 alloy is a common aluminum die casting alloy. It has exceptional mechanical properties and is used in hundreds of applications such as air brake castings, gear cases, and air-cooled cylinder heads.
Fluidity, pressure tightness, and resistance to hot cracking are just some of the A380 aluminum properties that are ideal for die-casting. Due to these properties, this 380 aluminum is extremely workable and machine-friendly for cutting or shaping processes. It also has excellent finish characteristics so your final product will look and feel like top-quality material.
A383 Aluminum Alloy
Another option for die casters is to use A383 aluminum alloy. This is alloy is typically only used when you are forming intricate components and require very specific die-filling characteristics. While it doesn’t share all the properties of A380, it does offer higher strength at high temperatures with less chance of cracking under heat.
A360 vs. A380 v. A383
To summarize the differences between the three types of casting alloys as outlined above, A360 has the best pressure tightness, high-temperature strength and corrosion resistance of the three alloys.
A380 is also highly corrosion-resistant but more cost-effective and easier to work with than A360, so this is the one you would use most commonly if you have budgetary concerns to consider and don’t need the highest levels of corrosion resistance or pressure tightness.
A383 is a modified A380 alloy you would only use if you need precise die filling that you are not getting from your A380 alloy, as it is not as durable as A380.
From the above introduction, you can know some details about the aluminum investment castings. If you have an inquiry on this item and aluminum die castings, welcome contact us freely.